A new, larger size of travelling column machining centre in the DMF range manufactured by DMG Mori has been introduced to provide even more versatile production opportunities within a machining envelope of 3,000 x 1,100 x 1,050 mm.
The modular DMF 300|11 with B-axis swivelling spindle head represents a redesign of the popular configuration that, compared to the previous series, has seen not only an expansion of 40 percent in the working volume, but also a 20 percent increase in rigidity of build.
The ±120-degree B-axis houses an integrated, 15,000 rpm speedMASTER HSK-A63 spindle as standard, but is available with a 20,000 rpm version, or with a 12,000 rpm powerMASTER spindle having higher torque at 288 Nm. All carry a 36-month warranty, irrespective of the hours the spindle has run.
The rigid table running the length of the DMF 300|11 accepts workpieces weighing up to 5,000 kg for 3- and 4-axis machining of large components. Alternatively, an optional partition can be inserted in the centre to allow safe pendulum machining of smaller parts, with set-up of the next job at one end of the table while production is in progress at the other.
Fully interpolative 5-axis machining can take place at either or both ends, or else in the centre, following the addition of one or two optional rotary tables set flush into the main table surface. Components weighing 1,200 kg can be accommodated and each C-axis may be ordered with a torque drive to provide the possibility of in-cycle turning operations at up to 700 rpm.
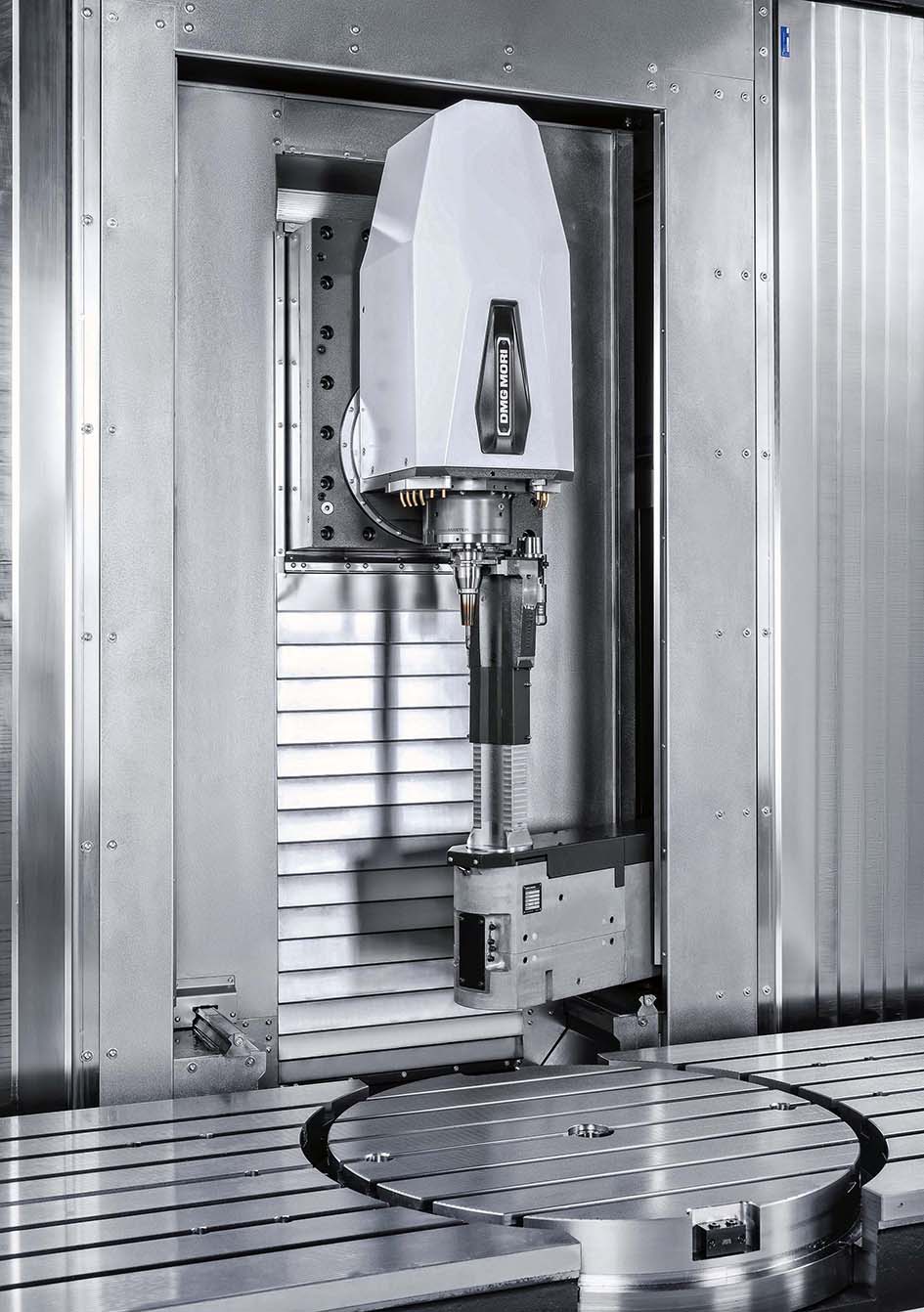
Tool change now takes place safely behind the work table, avoiding interference with fixtured workpieces and contributing to thermal stability.
Alternatively, it may be more expedient to add one or more A-axis rotary tables to enable 5-axis operations on horizontally-mounted parts weighing up to 500 kg. It is equally feasible to mount a static column or tombstone on the table for workholding, swing the spindle head through 90 degrees and use the DMF 300|11 as a horizontal machining centre with the added benefit of B-axis motion.
Tool exchange now takes place behind the table for increased reliability and this design alteration has been adopted in the smaller DMF models as well. Mounted inside the column, the standard tool magazine has 40 pockets for cutters up to 400 mm long. A larger magazine with capacity for 120 tools may be specified.
Rapid traverse in all axes using ballscrew drives is 42 m/min, although if optional linear drives are fitted in X and Y, the rapids are 80 m/min and 60 m/min respectively. Positioning accuracy is 5 µm thanks to the stable machine bed, three linear guideways in the X-axis and holistic cooling throughout.
A highlight of the cantilevered design of the spindle head is that the distance between the column casting and the centre of the spindle is always the same, irrespective of the position in the Y-axis. It ensures consistent rigidity over the entire travel, allowing users to program maximum power at any time, regardless of the transverse position of the spindle.
To ensure the DMF 300|11 remains a future-proof investment, DMG Mori is able to integrate the machine into digital infrastructures. Exclusive technology cycles increase machining productivity. Manufacturing becomes even more productive using automation, such as robotic loading and unloading, for which interfaces are pre-installed. All solutions for autonomous running are manufactured in-house, so the user has a single point of contact for the entire installation.
Leave a Reply