While many machine shops are enjoying the production benefits of robotic part handling, others are struggling to tackle the first steps of implementation. The capabilities of the Zerobot 100V eco, available in the UK and Eire from Leader Chuck International, can help provide manufacturers with the perfect starting point.
Within the machine shop environs the growing acceptance and popularity for robots is due to their material handling capabilities when loading and unloading parts into and out of machine tools and other manufacturing equipment. However, their effectiveness relies on correct implementation as Leader’s Managing Director, Mark Jones, explains: “Once the decision to implement this technology has been made some important questions need to be asked.
“Basically, these include: What are the maximum and minimum weights of the parts that will run? What condition are the parts in as they arrive (raw billet, casting, forging, pre-machined, size, sharp edges/burrs, covered in chips/coolant/oil)? Will the machining process be single operation or multiple operations requiring back working? How many parts and cycle times to define how long the infeed queue needs to be? Will it run lights out or will an operator be available to oversee the process? Any in-process inspection required? How much floor space is available for the automation? Will the capacity of this machine be taken up with the automation or will it be used without the automation for some of the time?”
At the heart of the loading system is the robot and different robots are designed for different kinds of environments. The Zerobot 100V eco is an industrial grade SCARA arm robot, a design that has become popular for machine loading in the manufacturing sector. It is designed to work in the swarf-covered, coolant-dripping environment encountered in the machine tool world.
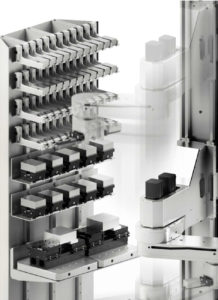
Double-sided raw material storage rack
Robots are usually specified by reach and payload. The Zerobot 100V eco can be specified with a right- or left-hand mounting of the arm with a radiused reach of 1.2 m providing enough range to access the whole worktable of most machine tools. While the 100 kg total payload means raw material billets or forgings up to 250 x 160 x 200 mm can be accommodated.
The infeed and storage of raw materials and finished workpieces is another area for consideration. Here, the Zerobot 100V eco offers a manually operated double-sided vertical rack system with the flexibility to be populated to exactly match the requirements of the components being processed. The double-sided rack design means finished parts can be removed and the raw material supply can be refreshed while the machine tool is operating, so downtime is kept to an absolute minimum. It also allows access to the machine’s working envelope if an unscheduled part needs to be manually loaded, supporting emergency repairs or rework scenarios.
End of arm tooling (EOAT), the tooling that is mounted to the end of the robot to assist in performing the necessary tasks, must be paid attention. “While various kinds of tooling, such as vacuum cups and magnets, are available for picking parts, the most common style on the shopfloor uses pneumatic grippers. As with the robot itself, quality grippers that are appropriate for the working environment are important. The standard Zerobot has the ability to automatically change the EOAT to suit the application, this is a quick, simple, manual procedure on the eco version,” Mark Jones confirms.
He continues: “The application will dictate the size and quantity of jaws and grippers that will be needed. Grippers are available in many configurations and may have two, three or four jaws. Two-jaw, parallel-close grippers are the go-to grippers for anything square, rectangular, or easily picked up between two fingers. Three-jaw grippers lend themselves to picking up round and hex parts, just as a three-jaw chuck is so prevalent on a lathe.”
The extensive range of Zerobot robotic automation systems means there is a solution available for almost every application. Starting with the Zerobot 100V eco with fixed double-sided rotating rack, no automatic gripper or automatic fixture change. Automatic rack rotation available as an option and, being such a straightforward design, it offers a simple I/O interface.
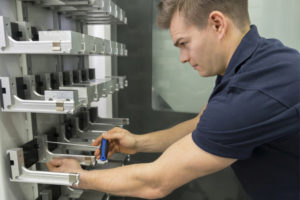
Material rack layout easily changed
to accommodate varying workpieces
Next is the Zerobot 100V featuring a double-sided automatically programable rotating rack, automatic gripper and fixture change options, and field bus interface with NC-program selection.
Offering two single racks that can be moved with a pallet truck, the Zerobot 100P has an automatic gripper and automatic fixture change option, with field bus interface for NC-program selection.
The most extensive of the Zerobot range is the 100S that comes with an additional linear axis for longer travel, two or more single rack systems that can be moved with a pallet truck, automatic gripper and automatic fixture change options, and a field bus interface with NC-program selection. When the additional linear axis for longer travel and more than two single rack systems are not required the 100S can be downgraded to the 100P system.
“The comprehensive range is a key feature for any workshop looking to dip its toes into the world of automation. It means the robot can be specified to support the different machine tools available, matching the needs of the business across the whole of the shopfloor. It allows production managers to gauge the real-world return on any potential investment making the decision to install dedicated automation systems that much clearer,” says Mark Jones.
He concludes: “Before the search for any articulating arm automation begins the basic details, we considered at the very start need to be understood. An honest look at these considerations will go a long way to defining an automation system that provides efficient and effective part movement. The answers to these questions will be important to both the supplier and the users on the shopfloor.”
For further informartion about Leaderchuck products please visit our website or email: