Robotic Handling Cells automate machine tool operation
Best known as a supplier of high quality manual, hydraulic, electro-mechanical and magnetic workholding equipment manufactured in Germany and Austria, including those marketed under the Hilma, Stark and Rivi brand names, Hitchin-based Roemheld UK will announce at MACH 2020 a significant diversification to its handling product range. Alongside workpiece manipulators, the company will launch from stand 430 in hall 7 a new suite of cells designed to automate machine tool tending and add extra processes beyond just workpiece handling and storage.
The ProModul concept from Hilma is centred on a core ‘R’ module, enclosed all-round for safety and equipped with a Fanuc 6-axis robot and two workpiece drawers. It provides a base level of automation for unattended production on CNC lathes, machining centres or other machine tools such as spark eroders. It also introduces the possibility of using a double gripper arrangement to progress components from Op 10 to Op 20 without manual intervention. Gripper exchange can be similarly automated to allow families of parts to be produced autonomously.
Where the system differs from others on the market is the availability of additional, dedicated, compact ProModul elements that can be positioned next to each other alongside the robotic handling module for performing operations such as deburring, measuring, engraving and assembly. The higher repeatability that is possible compared to an operator performing these tasks not only automates the processes but also tends to raise the quality of production.
The effect is to relieve the machine tool of these extra duties, which would otherwise consume time after the main machining cycle has been completed, yet still allow the user to benefit from complete machining of components. While it is possible to include some of these further operations in the main program, it is rare to find assembly tasks such as press-fitting incorporated into a machine tool.
Production output can be raised by combining more and more ProModul cabinets for completing the processes. Components are transferred between stages automatically by a variety of handling methods, according to requirements, and workholding is included as part of each package. Maximum workpiece weight allowable using the standard robot is 6.5 kg, although heavier duty models may be selected.
New Robot Gripper has services built-in
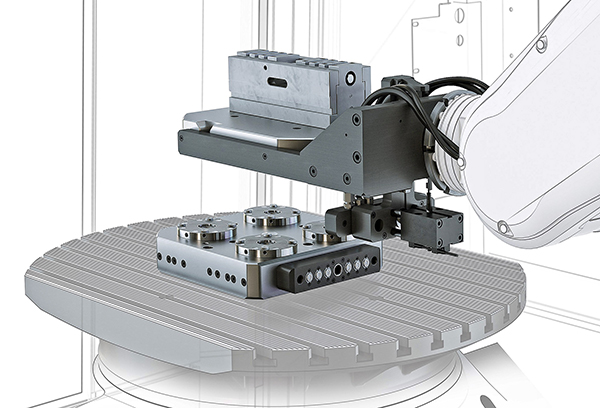
With the new Stark robot gripper from Roemheld, hydraulic, pneumatic and electrical supplies required for unclamping and clamping are transferred via a multiple coupling integrated into the pallet gripper
From the group’s Stark division and on show for the first time in the UK will be a robot gripper with zero point clamping for automated pallet exchange on machine tables without their own media supply. The services needed for clamping and releasing the workpiece, whether hydraulic, pneumatic or electrical, are all transferred to the clamping plate via a multiple coupling integrated into the robot’s pallet gripper.
First shown at EMO in Hannover last September, the system is supplied to suit the user’s requirements and is a cost-effective, entry-level solution to automated production that may be retrofitted at any time. Implementation is short owing to the system’s standardised coupling and flexible modularity. Process safety is assured by air blow removal of swarf and automatic checking of correct component seating, clamping and release.
Fail-safe pneumatic swing clamp
On display for the first time will be Roemheld’s pneumatically actuated swing clamps incorporating a mechanical locking action, whereby the full holding force – between 200 and 600 N – is maintained in the case of air pressure reduction or loss, ensuring operator safety and avoiding the production of scrap. Operating pressure is between two and six bar.
The clamp is a pull-type cylinder with a piston that is automatically locked when the workpiece height is within the designated clamping range, after which the air line can be depressurised or uncoupled, for example during pallet change. For unclamping, which is monitored, only the minimum pneumatic pressure is needed.
A feature of the clamps is a pair of flow control valves that can be easily adjusted from above. They allow the speed of the sturdy swing mechanism to be reduced if the flow rate is too high or when the clamping arms are of larger mass. It also enables synchronisation or sequencing of the closure of several connected clamps. Swing angle is normally 90 degrees clockwise or counter-clockwise, although it can be 60 degrees, 45 degrees or absent (0 degrees).
If machining dry or with minimum quantity lubrication, the wiper can be protected from the ingress of small particles by an additional wiper ring.
Vices for 5-Axis machining to include floating clamping point model
Two vices designed for workholding on 5-axis machining centres will be exhibited. The Hilma MC-P is able to grip on just 3 mm of material, reducing raw material costs, and offers high stability and precision combined with excellent accessibility and comprehensive chip protection. The compact design enables collision-free tool paths and the use of short, standard tools for multi-axis machining.
Offering centring or clamping functionality, it is suitable for a wide range of applications including securing long components and housings made from cast materials. Mechanical and hydraulic versions are available and jaw widths range from 40 to 125 mm, with maximum clamping forces of 8 kN to 35 kN.
Another workholding system appearing for the first time at a MACH show will be the division’s range of three MC-P Z Balance vices, which have a floating clamping point to avoid stressing or deforming the component being secured. After operation of the spindle, clamping range being from 6 to 400 mm according to model, first the two slides concentrically approach the workpiece. When the first jaw reaches it, just the second jaw advances until they are both in contact with the component. Only then is the desired clamping force applied.
Pressworking and Moulding Products
From its position within the Metalforming Machinery Makers’ Association’s metalworking village in hall 20, stand 631, Roemheld will promote ther group’s wide range of products aimed at the pressworking and moulding industries, including die clamping systems, handling carts, carrying consoles and roller and ball bar elements.
New to MACH will be the Industry 4.0 press system Flexline for automatically clamping almost any die on the ram of a wide variety of press models. It uses integrated sensors to measure real-time data on holding forces and transmit the information to the machine control.
The operator has access to information concerning the actual clamping force on the die and is immediately able to detect overloads, the occurrence of unusual forces during operation, and die wear and breakage. The system, which is suitable for either factory installation or retrofitting, facilitates error analysis and enables rapid problem-solving when servicing is required.
Roemheld’s Rivi division, a manufacturer of magnetic clamping plates for securing dies and moulds, will stress its pedigree as a supplier not only to the plastics injection moulding sector but also unusually to the rubber industry. The customised M-TECS products are uniquely able to withstand elevated temperatures up to 240°C encountered in such presses and can generally be retrofitted within a few hours.
Dies and moulds made from ferromagnetic materials can be clamped and subsequently released over their full surface area and high plate stiffness resists bending. The systems work without electrical power and require only a short current pulse lasting a few seconds to activate and deactivate the magnets.
Permanent magnets generate a field that penetrates a few millimetres into the tool and hold heavy mould halves weighing several tons in the correct position, bringing them together with absolute parallelism. Even moulds with complex geometries can be precisely clamped without deformation. Uniform distribution of the clamping force ensures low die wear.
Visit Roemheld UK at MACH 2020 in Hall 7, Stand 430
or visit www.roemheld.co.uk