Lawrence Engineering was formed in 1985 by Michael Lawrence who is a tool and gauge maker by profession and who started his career in engineering back in 1970.
Starting off by himself as the sole employee, and initially working from his garage, the company that’s located at the foot of the Ox mountains near Sligo in Ireland now employs 14 people and is growing rapidly. 95% of Lawrence Engineering’s business is to medical device manufacturers located in Ireland. The company whose policy is always to invest in the best and newest technologies has a wide range of machines including assorted EDM machines, milling machines, grinding machines and turning machines and specialises in manufacturing very high precision, low batch, ground components in a variety of materials and in particular small injection mould and extrusion tooling.
In order to meet his customers’ demands Michael Lawrence has spent in the region of £800k this last year on assorted machines including the purchase of the Rollomatic NP5 grinding machine which is his companies biggest single machine purchase to-date. Several machines are now under order and a new purpose-built factory extension of 200 sqm is being constructed to house them. The enquiry level for January 2019 was equal to that in whole of 2013 which demonstrates how many more engineering companies are looking to Lawrence Engineering to supply them with components. Michaels son, James, who joined the workforce around 4 years ago is helping oversee the rapid expansion over recent years with overseas sales to countries as far away as Canada now being made.
Michael Lawrence had not heard of Rollomatic before he saw the latest NP5 Grinding machine on the AGS stand at the Mach show last April. Having received a demonstration at the show he immediately understood the advantages that the machine would bring to him and soon thereafter placed an order for a high specification of Rollomatic NP5 machine that also caters for special un-round profile grinding.
This machine, along with the others in Rollomatics wide range of grinding machines is manufactured at their 12,000 m² production site located in Le Landeron, Switzerland, that incorporates ultra-modern manufacturing equipment and technology.
Michael was very impressed with the very large saving on cycle times that the Rollomatic will bring to Lawrence Engineering that, in some cases, will reduce the time to programme and manufacture a very special tool from over 2.5 hours to just 10 minutes. Furthermore, because tools on the Rollomatic machine are produced in a single automatic operation from the solid bar material, this guarantees the highest possible precision and removes the need to transfer parts across several different machines which was previously the case.
Programming could not be simpler with Rollomatic’s software, which works offline or directly on the grinding machine allowing the most complex of tools to be programmed up in just 5 minutes. The NP5 uses the special design of pinch/peel grinding pioneered by Rollomatic that allows parts with high length to diameter ratios to be manufactured with component part lengths up to 400 times the part diameter to be ground without deflection issues. The machine has a working range for parts from 0.025mm to 25mm in diameter with autoloading from pallets via an integrated 3-axis robot loader. The 5-axis machine allows for stepped diameters, angles, chamfers, flats and even hexagonal and non-concentric cam profiles to be ground with ease.
The software in conjunction with the rough and finish grinding wheels set up allows users to specify multi-pass grinding operations for roughing and/or finishing to achieve the highest possible level of accuracy whilst creating superior surface finishes on tapers and radii. Size control across large batches is within 0.002mm on even the longest of tools with runout concentricity of under 0.001mm from this high precision grinding machine. Movomatic and Marposs gauges are used for part positioning and for the post-process automatic gauging of ground diameters with automatic feedback to the Rollomatic machines Fanuc control.
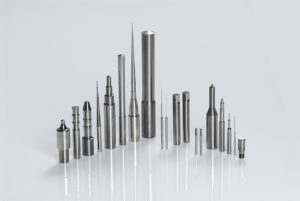
Typical parts ground on Rollomatic NP machines
As with all Rollomatic grinding machines the NP5 comes with the industry leading 3 years parts and labour warranty as standard and with free software updates for life to ensure that all Rollomatic end users are always kept ahead of the game.
Chris Boraston, MD at Advanced Grinding Solutions is naturally delighted with the sale of the Rollomatic machine to Lawrence Engineering commenting that this is precisely the type of new customer that AGS are looking to add to Rollomatic’s already impressive UK and Irish customer base. With more rotary tools of all kinds being manufactured on Rollomatic’s here in the UK and in Ireland than on any other make of grinding machine they are of course one of the leaders in their field and in the last year we have been able to add a number of new customers that have become Rollomatic end users for the first time and this is especially pleasing. The Rollomatic NP3 and NP5 machines are the firm favourite for tool manufacturing companies and it’s good to see other forms of specialist makers of tools and punches investing in these machines to increase the precision of their parts and to drastically reduce their cycle times.
Advanced Grinding Solutions, Sole UK agents for Rollomatic, may be contacted on 0044 (0)2476 22 66 11 or via their website www.advancedgrindingsolutions.com