The worlds of CAM and tooling have combined to deliver significant cycle time savings across a wide range of applications, including mould and die, turbine blade, impeller blade and blisk production. Combining Open Mind’s HyperMILL MAXX tangent plane machining strategy with circular segment cutters (Barrel Milling cutters) from WNT, it is feasible to reduce milling cycle times by as much as 90 per cent when semi-finish and finish milling on five-axis simultaneous machining centres, with the additional benefit of reducing load and stress on a machine’s spindle and improving surface quality.
The Open Mind tangent plane machining strategy, which is only available through its HyperMILL Maxx CAM system, was developed in conjunction with Circular Segment or barrel milling cutters in mind. The large radii ground on these cutters (up to 3000 mm) allows much greater step overs between cutter paths to deliver reduced cycle times. However, to achieve this improvement as well as maintaining, or improving, surface quality the cutters have to be moved simultaneously in five axes in a sweeping/pendulum-like motion over the workpiece. The HyperMILL MAXX user interface simplifies these complex movements making them easy to program and maximises the cutter geometry to present the cutter at the optimum orientation to the workpiece at any point on the cutter path.
The resulting benefits of the Open Mind milling strategy and WNT’s circular segment cutters are:
- Increased step-overs but generating the same theoretical scallop height
- Improved cutting performance in difficult to reach areas of a component (pockets etc.
- Much greater machine efficiency
- Reliable finishing strategies and process security
- Reduced thermal deformation
- Fewer tools required
Working in partnership with the CAM software is the design of the WNT Circular Segment Cutters, which have been developed to enable machining with a larger tool path distance during pre-finishing and finishing operations. There are four types of cutter in the range, these being Barrel-shape, Oval Form, Taper Form and Lens Shape, with the following main application areas being targeted for their use: turbine blades; impeller blades/blisks; and mould tools. The key feature of these end mills is the large radii in the cutting area, which simulates a ball-nose cutter with a cutting diameter equivalent to between 12 and 3000 mm. This design opens up new opportunities for high performance machining, when combined with Open Mind’s HyperMILL MAXX CAM software.
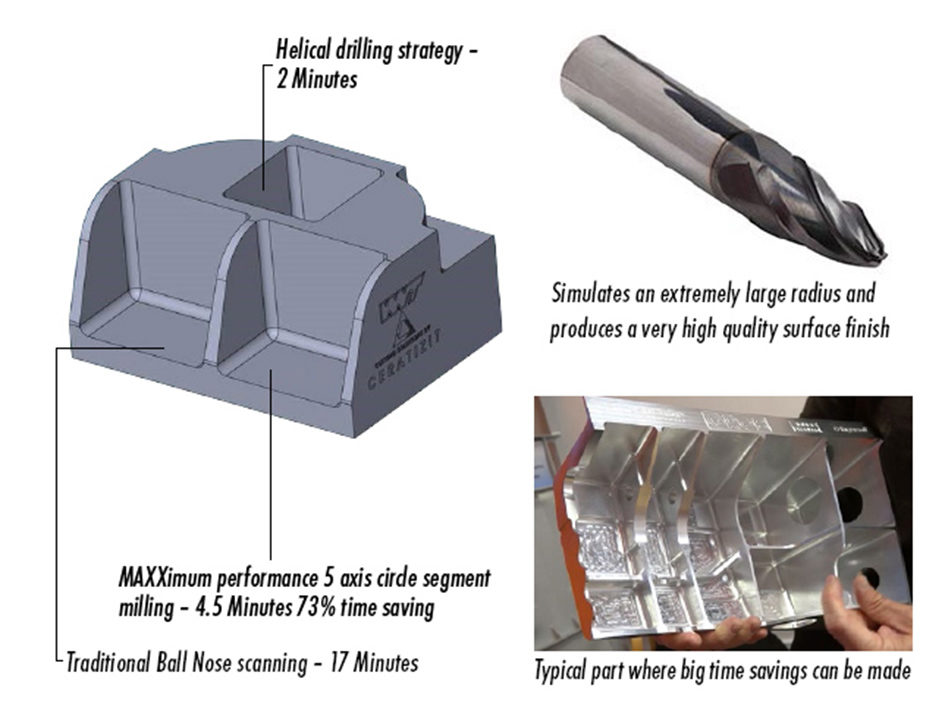
The combination of circular segment cutters from WNT and Open Mind’s software is generating
significant cycle time savings
The result is significant reduction in cycle times with the added benefit of improved surface finishes as the extremely large radius enables greater step-over distances to be achieved. In comparison, using a typical ballnose cutter the step-over distance (or axial depth of cut) would be 0.5 mm and surface finish would equate to around Ra 1.22 micron. Whereas, with a circular segment cutter this step-over can increase to 1.5 mm, while at the same time surface finish improves to Ra 0.46 micron. Typical cutting data for a 6 mm diameter circular segment cutter with three flutes machining tool steel (1.2312) will be 300 mm/min surface speed, 16 m/min feedrate and an axial depth of cut (ap) of 1.5 mm and radial depth of cut (ae) of 0.2 mm.
Furthermore, the circular segment cutters are ideal for machining hard to reach planes on a component, such as deep walls in a pocket on an airframe or mould tool that would be impossible to reach for conventional end-mills. Depending on the size of tool selected step-over can be as great as 7 mm, which using a conventional ballnose cutter would be just 0.4 mm. it is this increased step-over, without any loss in surface quality that sees the dramatic cycle time reductions being achieved. The same cutter can be then used to perfectly blend the corner radius of the component. In addition to long-edge machining of component walls, or turbine blades the end of the cutter can be brought in to play to finish machine to base of a pocket, again with the large step-over benefits as before reducing cycle time.
Toolholding also plays an important role in maximising the benefits of circular segment milling and the initial recommendation from WNT is to use its Centro-P collet system, although its hydraulic and shrink fit systems will work equally as well. The precision of the high performance Centro-P chucks and collets means that users can maximise the productivity of solid carbide cutters. Runout of the system is guaranteed at 3 micron and are balanced to G 2,5 at 25000 min-1 and U ≤ 1gmm. Using the latest OZ-style collets which can grip cutters between 3 and 25 mm diameter to fully utilise their metalcutting capacity thanks to the additional gripping power of up to 350 Nm available.
A video highlighting the benefits of circular segment milling can be found here: https://www.youtube.com/watch?v=BMvCd87jfAw
WNT and Open Mind have also worked together on a similar machining strategy, that of helical drilling. Making use of standard solid carbide end mills, or indexable insert face mills, using the complex motion available from simultaneous five-axis machining centres it is possible to produce deep cavities from solid material in a very short space of time. The cutter is presented to the workpiece at a tilt angle to avoid machining with the end face, thereby eliminating any issue with lack of surface speed at the centre of the cutter. There are a number of major advantages to using this process, The first being that the cycle time to produce holes, whether they be round or square (or any other shape) can be reduced by 20-25 per cent. Secondly, the process using Open Mind’s HyperMILL MAXX means that only a single cutter is required to produce different diameter/shape holes in a component. As swarf removal is more efficient using this method the surface finish is improved while stress on the cutter is reduced.