It is not unusual for precision sub-contract machinists to be ‘sworn to secrecy’ over contracts they are involved with as either one-off ‘special’ jobs or, indeed, production schedules that stretch over the long term. Cosmopolitan Engineering is a case in point, with the Sheffield-based company continually securing and processing a number of contracts that include workpieces destined for high-profile manufacturing projects. The work includes supplying blue chip clients throughout the UK, including names such as Sheffield Forgemasters International and RTM Power.
As befits the company’s accreditation to ISO 9001, the project list has/does include all manner of components, of every size – from precision one-offs for marksman’s guns, to steam traction engine parts and nuclear project work.
“We simply can’t talk about most of the jobs,” says Production Manager Mark Leonard. “Which is a great shame, not least because the complexity of some of the final-build projects would really show how small, highly-skilled engineering companies such as ours continue to play a crucial role in creating awe-inspiring engineering spectacles that are the envy of the world.”
In addition, the lack of publicity surrounding such work often disguises the fact that Cosmopolitan Engineering – an established (for more than 30 years) supplier of parts of all sizes and in all metals, including tool steels and titanium – cleverly utilises a portfolio of sophisticated CNC machines to turn, mill, drill and grind workpieces that consistently meet customer demands for high-quality components that are supplied to schedule and in the most cost-effective way.
A quartet of machines supplied by T W Ward CNC Machinery (Ward CNC) plays a key role in enabling the company to consistently meet these demands.
Installed progressively, the trio of Hyundai-Wia turning machines – L400LMC lathe with C axis and driven tools, SKT-300 turning centre and a L300C two-axis lathe – together with a Hartford Omnis 1020 vertical machining centre, have enabled the seven-employee firm to consistently meet the demands of customers throughout the UK and across all industry sectors.
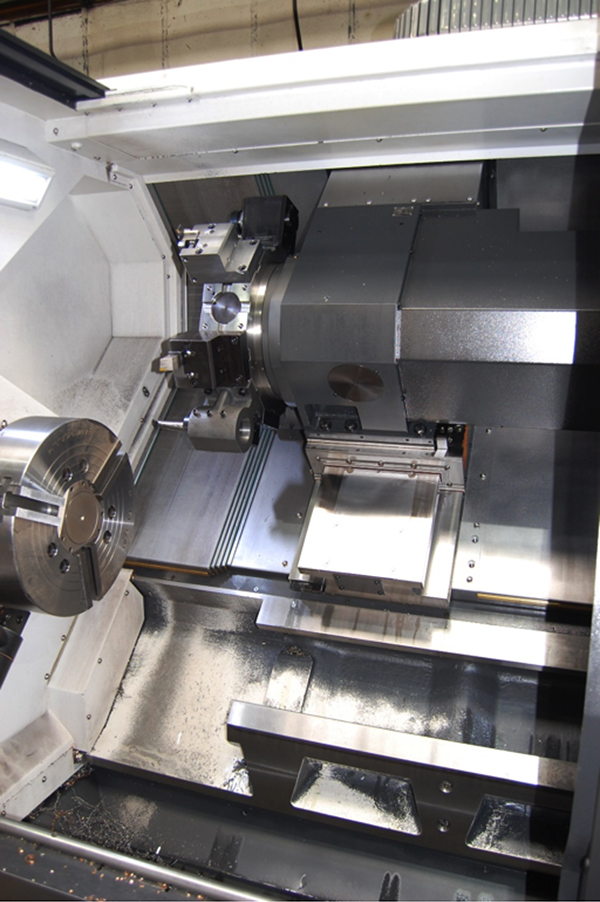
The working area of Cosmopolitan Engineering’s Hyundai-Wia L400LMC lathe with C axis and driven tools
Many of the components produced on these are one-offs or in small batches of up to ten. However, one particular on-going large contract for the volume machining of a family of axles demonstrates how the Ward CNC-supplied machines combine to good effect.
Produced from EN24T billets, the axles range in size from 100 mm diameter to 290 mm long and 120 mm diameter to 610 mm and 937 mm long. All three sizes are turned to diameter then, on the shortest version, a grease nipple hole is drilled and a 16 mm wide by 20 mm deep cross slot is machined by the SKT-300.
On the two larger sizes, which are machined on the two metre bed L400LMC with C axis and driven tools, a screw thread is generated before, on the largest component, a keyway is produced measuring 32 mm wide by 16 mm deep and 140 mm long on the Omnis vertical machining centre.
The axles all fall well within the machines’ capabilities: the SKT-300 has a maximum turning diameter and length of 560 mm and 720 mm, respectively; the L300C with 500 mm and 720 mm, and the L400LMC has maximum turning diameter and length capacities of 570 mm and 2,100 mm. The Omnis has X, Y and Z capacities of 1,020 mm by 510 mm by 510 mm.
The axles – part of an ongoing contract to supply a prestigious engineering project in London – are then supplied to the customer ready for assembly.
Mr Leonard, who has been Production Manager at the company for over two decades, says the machines have never let Cosmopolitan Engineering down. “We have been dealing with Ward CNC for many years, working with the applications engineering department to machine/manufacture items such as tool posts, to accompany new machine (lathe) sales.
“In this time we have become very familiar with the ranges of machines that Ward CNC held in stock and when we needed CNC capacity, Ward CNC was the logical choice. The Hartford vertical machining centre was our initial installation, followed by the Hyundai-Wia SKT-300 and L300C then, most recently, the L400LMC.
“Importantly, the Hyundai-Wia machines are all powerful, geared headstock machines – with a 22 kW spindle motor on the L300C, 26 kW on the SKT-300 and an impressive 30 kW with the L400LMC. These spindle ratings combine with a quality of construction that promotes rigidness and accuracy (for example, to 3.5 microns on the SKT-300), plus minimal downtime. And that’s so important.”
He concludes: “As each machine has been installed and put into service, we’ve obviously noted its reliability and, subsequently, each time we needed to expand our CNC portfolio we didn’t have to worry too much about the quality of the machines or the back-up from Ward CNC nor, indeed, the cost-effectiveness of the packages on offer.
“We ideally like to have one operator running two machines, so commonality of CNC systems (Fanuc) has been a factor in our choice of machines, although the support on offer from this local supplier takes some beating.”