Established in 1995 and located in County Cork, southern Ireland, Maas Precision Engineering not only manufactures and supplies machined parts and components to a variety of customers and industries, but also offers design, prototyping and product development as additional services. The firm’s motto is “dimensionally correct, cosmetically perfect”, on the basis that components must look aesthetically pleasing as well as being accurate and functional.
As far as CNC milling is concerned, it is carried out on seven Hurco vertical machining centres (VMCs). The first was supplied more than 20 years ago and is still running today. All quantities are catered for, with Maas manufacturing anything from one-offs and small batches up to volumes of 20,000 or more.
Managing director Tadhg Hurley said, “We owe our business success to Hurco and are confident in the machines. We know we can turn parts around quickly, making prototypes in one day or a maximum of two days. Every person here can program every machine.

The Hurco VMX30Ui 5-axis machining centre at Maas.
“Whether it be a 20-year-old machine or a new 5-axis model, we usually program directly at the machines and can process orders really quickly because we know they are going to be right”.
The machines play their part, but Maas is clearly a well-managed business that is committed to training its people and to making the right investment at the right time. In 2018 it purchased its first 5-axis VMC, a Hurco VMX42SRTi with swivelling B-axis and rotary C-axis set in the table. The main benefit was that more operations could be completed in a single set-up.
The versatility of the machine design allows it to be used as a full-capacity 3- or 4-axis machine when needed. For 5-axis work, some additional training was required so that operators learned the axes of rotation and how to set up parts. 5-sided and 3+2 jobs can all be programmed at the Hurco Max 5 control using the same easy-to-use conversational prompts that are employed for 3-axis applications.
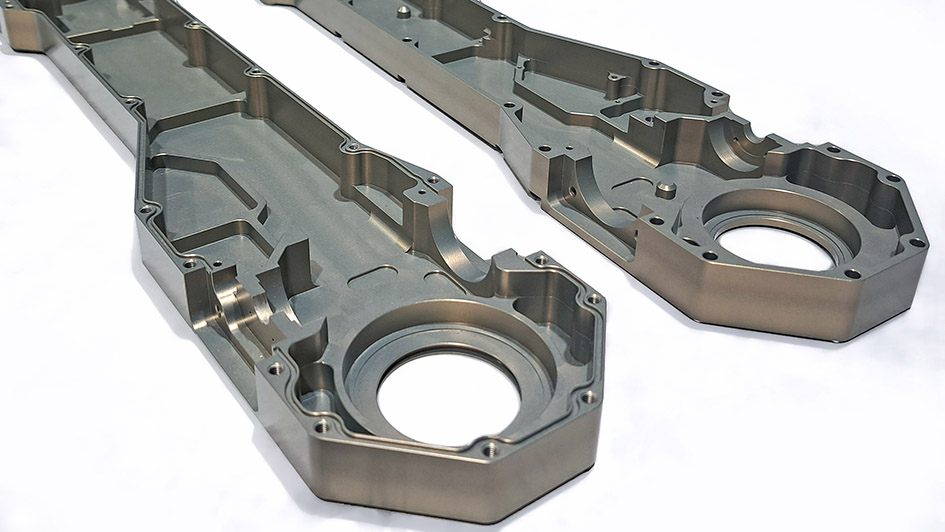
ROV arms machined by Maas on the Hurco VMX42SRTi using 3- and 4-axis strategies.
The transition to 5-axis machining was clearly a success as a second 5-axis model has been installed, this time a Hurco VMX30Ui of more compact design with a swivelling trunnion carrying a rotary table.
Programs can easily be transferred between the Hurco machines, new and old, to balance capacity utilisation. Maas needs to be able to respond quickly to changing customer demands, so knowledge that production runs can be readily swapped between machines helps to build confidence that challenging targets can be achieved.
Production manager Dale Thomas describes a variety of components manufactured by Maas for a remotely operated vehicle (ROV) used in bomb disposal. Many of these parts are made on a 5-axis Hurco machine, avoiding the need for additional fixtures that would be required if only three axes were available.
For example, the arm for an ROV that previously required six set-ups was moved to a 5-axis machine. Production time was reduced significantly, shaving several hours off the run. There is a lot of metal to remove to minimise weight, whilst retaining strength. Parts are programmed either offline or directly at the machine control, with considerable benefit derived using the Ultipocket and DXF software options, which are on all the Hurco machines at Maas.
Leave a Reply