GF Machining Solutions’ fully automated manufacturing cells that integrate multiple advanced process technologies provide a way forward for medical manufacturers.
Whether producing consumables, implants or surgical tools, the challenges facing medical component manufacturers today are many and varied, and include -: continuously shrinking batch sizes, increasingly complex geometries and tighter component tolerances. Occurring in high-mix/low-volume production environments (HMLV), many of these challenges reflect the growing trend towards minimal invasive surgical procedures and the need to manufacture implants and devices that are bespoke and patient-specific.
A way forward for the manufacture of bone saw guide blocks, pioneered by GF Machining Solutions, involves a turnkey solution and the development of secure and reliable machining processes that combine the company’s high-speed milling, wire EDM and laser texturing machine tool technologies with advanced tooling and automation (i.e., robot and workpiece pallet systems), to create fully automated, and flexible, manufacturing cells. The approach ensures medical component manufacturers’ compliance with ISO 13485 medical standards and the ability to meet complex part geometry requirements.
Bone saw guide blocks
Made from vacuum-hardened 45HRc 17-4 stainless stell, bone saw guide blocks are used to position surgical saws during hip, knee and shoulder replacement procedures and require complex curved surfaces and matt finishes, along with smooth and accurate guide slots. The big challenge is that the guides must match the shape of the individual patient’s bone.
To meet the stringent quality standards involved, that include tough industry regulations and traceability requirements, and fast turnaround times, the GF Machining Solutions’ turnkey approach is driven by the company’s System 3R Work-Shop-Manager (WSM) software which acts as a digital command centre distributing production orders and managing parts and data, while identifying each pallet through integrated radio-frequency identification (RFID) chips.
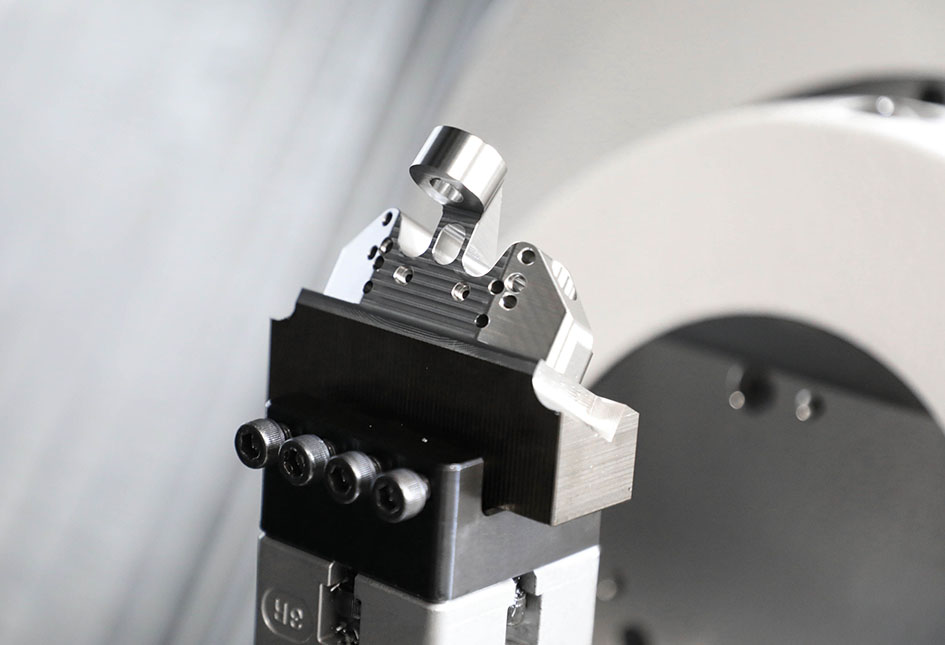
Bone saw guide block on GFMS MILL X 400 U
Working with the software, the pallets and zero-point chucks employed in the solution allow manufacturers to position workpieces accurately in the different machining systems used.
The process begins with raw material mounted on the pallets. Then, a coordinate measuring machine (CMM) measures the offsets which are then assigned to each pallet before being transferred to a SQL database within Work-Shop-Manager. Other information, such as raw material references and operator ID, can also be stored in the database.
Pallets enable manufacturers to automatically load/unload work in seconds using a robot for ensuring reliable positional repeatability.
Once pallets re loaded, they move, first, to a Mikron MILL X 400U high-speed 5-axis machining centre to machine the profile and part features. The machining centre used in the cell has direct-drives on all five axes, a 42,000rpm StepTec spindle and a rotary tilting table with 220 degrees of tilt.
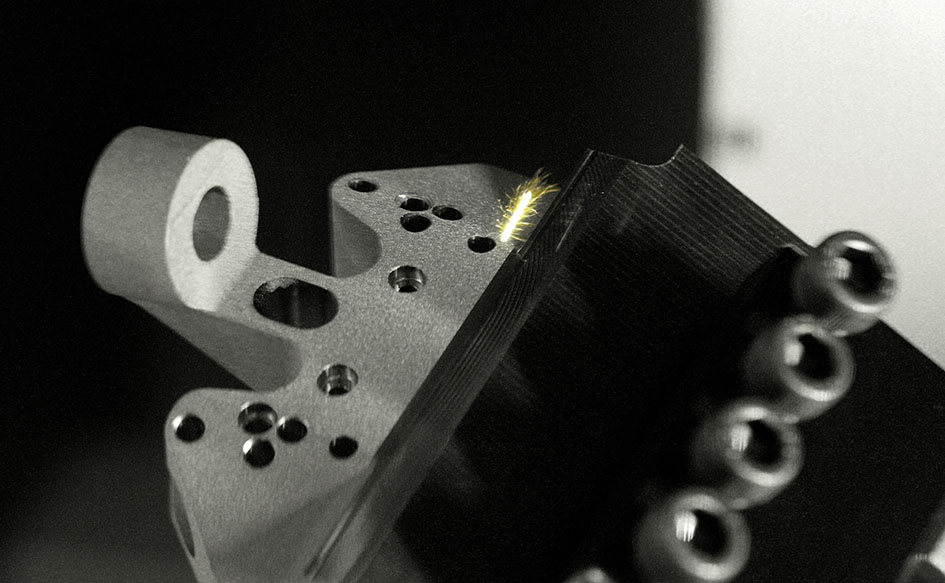
Bone saw guide block on GFMS Laser P 400 U
Milling cycles are 46 minutes long and surface finishes generated are < Ra.07µm.
The high-surface finishes achieved can be explained, in part, by the machine’s table tilting range which allows good access to guide block, from all sides, enabling the use of shorter tool that reduce vibration and deliver longer tool life.
The machine also features integrated Automatic Machine Calibration (AMC) hardware and software that ensures high accuracy machining even when difficult conditions prevail; machine calibration takes only a few minutes and does not require specialist staff.
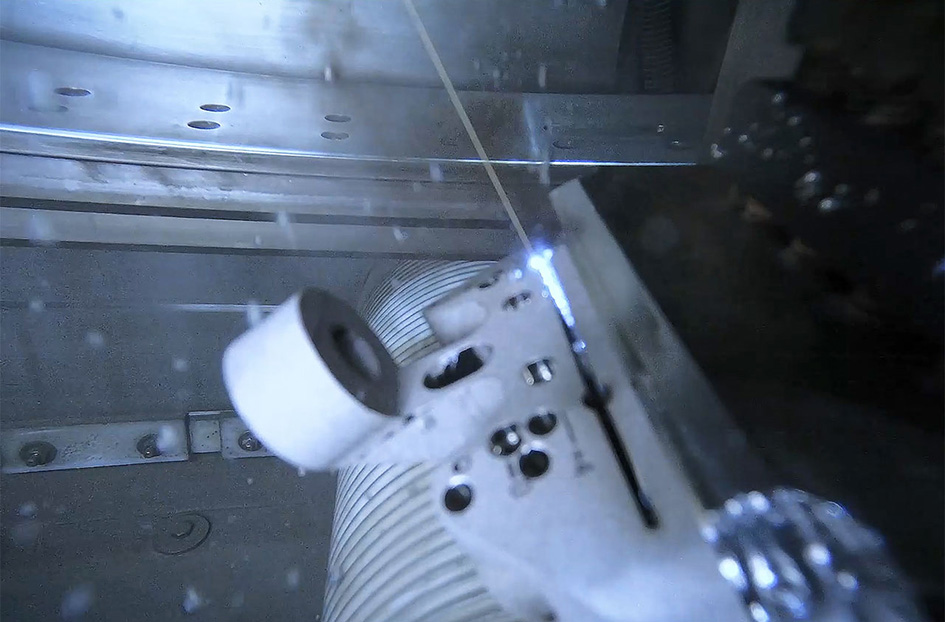
Bone saw guide block on GFMS CUT P 550
To machine the performance-critical slots that ‘guide’ bone saw blades during surgery, the cell features a high-performance WEDM machines – an AgieCharmilles CUT P 550.
The machine makes angled cuts at both at both edges of the slots and is a challenging operation owing to curved features which alters the amount of material being removed during the cut. To ensure precision and speed, the machine’s onboard ISPS (Intelligent Spark Protection System), which automatically analyses and adjusts each spark’s position, duration and intensity in real time, in-line with part features, is employed and controls the quality of the cut.
The CUT P 550’s QUADRAX design and low thermal conductivity and good vibration dampening ensure positional accuracy and repeatability.
The next stage in the process uses a laser texturing machine.
Bone saw guide blocks need to have a matte, non-reflective surface that prevents glare when being used in operating theatres by surgeons. To achieve this, and also enable critical information for traceability purposes to be machined on the parts, a LASER P 400 U (5-axis) laser texturing machine is used.
The laser machine helps eliminate manual operations i.e., masking/de-masking and grit/sand blasting to achieve the desired surface finishes. As well as being faster, the use of a digital laser is also cleaner and less prone to human error.
Summary
Fully-automated turnkey cells deliver significant benefits to medical manufacturers. The integration of a number of machining/production process (milling, EDM, laser), controlled and monitored from single control centre delivers high part quality, process efficiency and 24/7 production capacity.
Leave a Reply