Proform Laser, situated on the Wirral, started out in business as a laser cutting subcontractor in 2016 when they purchased a laser cutting system and a press brake from Bystronic. With a successful and growing business, the company was confident to buy two more laser cutting machines, the most recent being installed in January. As a fully functioning laser job shop, certified for Aerospace to AS9100, Proform was also working on automotive parts for JLR and other industries at the time of the first coronavirus lockdown in March 2020.
As the lockdown started to bite, there was disruption to the normal level of incoming orders at Proform for a few weeks, owing to the shutdowns at various manufacturing sites (especially in automotive and aerospace sectors which responded to the travel bans and furloughed most of their employees).
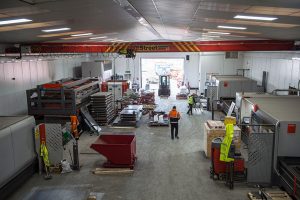
Production within Proplates facility on the Wirral
The Proform Group is run by the Canner family, father Russ, daughter Laura and son Mike, who are all keen gym members and like to keep in shape. Seeing an opportunity with gyms closed and people unable to access the equipment needed to work out, they decided to make some standard products for weight lifting. To make these plates is a very simple and rapid operation using laser cutting, no bending or welding is required, only some minor finishing when they come off the laser cutter. In contrast a typical automotive chassis consists of 200 parts which need cutting, forming, welding and finishing. Plates are made from mild steel sheet of a thickness of 20 mm and have a central hole and some optional features like handles easily produced on the laser cutters.
Initial production started in a low-key way with sales mainly to family, friends and by word of mouth. Realising the market demand for home equipment during lockdown the company re-arranged itself and launched the Pro Plates brand with a dedicated website for online ordering and started building a large following on Instagram and Facebook. Recognising that enthusiasts love nothing more than to upload photos of their newly-purchased weights online and tag the company that supplied them, some of the best sales leads come from delighted customers.
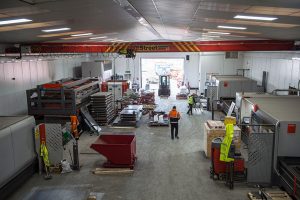
Onsite Laser cutting and bending
Growth has been outstanding and the idea that they might make £ 10,000 out of the idea is now a family anecdote. During the past year, the company has employed an additional 50 staff and is finding that keeping pace with the order intake is a challenge. By January 2021, 6,000 orders had been received via the website and 5 staff are employed to look after the social media content, advertising and marketing. Another 5 staff are employed for customer service and two 40 tonne articulated lorries arrive daily to dispatch completed orders.
The numbers are staggering, and a truly good news story for UK manufacturing. Since May 2020, the business has quadrupled in turnover where many other subcontractors have struggled to keep busy. In one month recently, Pro Plates turned over more than a full year of revenue in 2019 for Proform Group. Each week the company turns 70-80 tonnes of steel plate into steel weights. The product portfolio continues to grow with the addition of powder coating, customised designs and accessories like bars, racks and powercages allowing the home user to kit out their garage or garden shed with everything they need to pump iron. An opportunity to fill a gap in the market, with Chinese weights held up in shipping containers around the world, has led to a quick delivery and lower price than gyms have traditionally paid for their equipment from traditional wholesalers, with some products 70% cheaper than historical competitors.
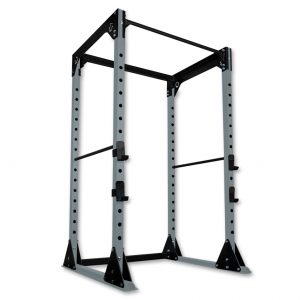
Powercages to complete your home gym
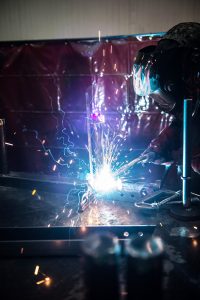
Production all in-house, design, cutting, bending, welding
Plans to expand into shipping weights to Europe are on the back burner until they can keep pace with the UK demand. The added bonus of “buying British” is an added attraction to set Pro Plates apart from other suppliers.
The whole factory layout has been modified to suit the workflow of Pro Plates and plans for a factory extension into the yard of the current facility are in hand. At present the factory is running at full capacity, including a night shift and a full sheet of 20 mm steel weighing 750 kg is cut in an around an hour on the high speed fibre laser cutting machines from Bystronic.
When asked about why she chose Bystronic for the equipment, Laura Canner said “We went on the UK study tour to the manufacturing site of Bystronic at Niederönz in Switzerland and were impressed by the Swiss expertise, the price point for the equipment and the smart red colour of the machines.” Although other vendors were evaluated, Bystronic were chosen and the nesting software used throughout is the BySoft platform from Bystronic.
In a time of bad news stories around the world it is very satisfying to share the news of a UK manufacturing business supplying UK customers and growing to employ more people in a region where manufacturing has been hard hit for many decades.
For further information about Bystronic products please visit: