In August 2020, a pair of BT40 vertical machining centres (VMCs) built-in Taiwan by Leadwell was supplied by UK and Ireland agent WH-Lead (www.wh-lead.co.uk) to the Holmfirth factory of HB Bearings (www.hb-bearings.com), which less than a year previously had increased its turnover by one third through the acquisition of Gamet Bearings.
Low-volume manufacture of both bearing ranges, which include precision radial, taper roller, deep groove ball, cylindrical roller and angular contact as well as many other types, is being consolidated in the Holmfirth factory, where a purpose-built extension has been added to house some of the production equipment from Gamet Bearings.
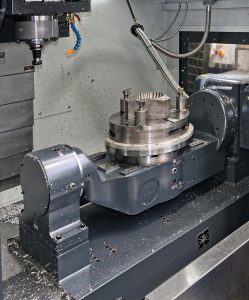
The trunnion arrangement on the Leadwell V-40iT 5-axis machine is wide enough to accommodate a 680 mm workholding fixture for a 636 mm diameter bearing cage.
The new Leadwell machines, a 4-axis model with rotary table and a 5-axis trunnion-type machining centre, were bought to strengthen production capacity for manufacturing the high precision, bespoke bearings in metric and imperial sizes. A wide range of materials are involved, including stainless steel, tool steel, plastics, bronze, aluminium and exotic alloys. The bearings are often specials, new designs or obsolete types that may need to be reverse-engineered to keep old manufacturing plant, steel mills, mining equipment, oil rigs or classic cars in operation.
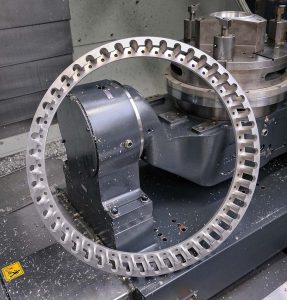
The machined 636 mm diameter bearing cage.
Graham Hirst, managing director of HB Bearings / Gamet Bearings commented, “We have prioritised the purchase of these Taiwanese machines ever since we bought our first one, a machining centre, more than 25 years ago.
“We sold it when the two new machines arrived, with a view to pre-empting its eventual failure. However, right to the end it still milled dowel holes in 62 Rockwell steel to within 10 microns.
“We now have five machining centres from Leadwell and three of their lathes, including two recent models installed in August 2017, which are just as well-built, accurate and reliable.”
Purchase of a second five-axis machining centre for the factory, a Leadwell V-40iT, was down to a desire to supply increasingly complex bearings, especially to the motorsport sector, in ever shorter lead-times.
Some products have complex flanges and profiles that need simultaneous interpolation of all five axes for their production. Others have angled holes that benefit from using the machine in 3+2-axis mode. By automatically repositioning the component using the rotary axes, production can be completed in, for example, two operations rather than the four that would be needed on a 4-axis machine, reducing the manufacturing cost.
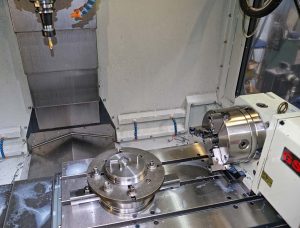
Working area of the Leadwell V-30iF, showing the 4th axis and possibilities for Op1 / Op2 machining.
The V-40iT was selected partly due to its competitive price for an 846 x 635 x 488 mm capacity 5-axis machine having a 12,000 rpm / 18.5 kW (24.8 kW-30min) BBT spindle with through-coolant and a 40-tool magazine. Additionally, the generous width between the trunnion bearings makes it possible to accommodate on the 350 mm diameter table a 680 mm fixture for holding a 636 mm diameter bearing cage.
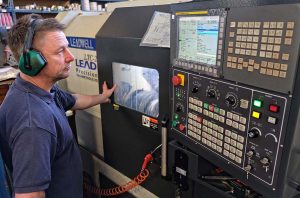
One of the Leadwell CNC lathes in the Holmfirth factory, an LTC-25iL installed in the summer of 2017.
It was the other new machining centre, a V-30iF four-axis VMC with 800 x 460 x 510 mm working envelope, that replaced the similarly sized, 25-year-old machining centre. The latest model has a 12,000 rpm / 11 kW (14.7 kW-30 min) spindle with through-coolant and 24-tool ATC.
Nearly all programming is carried out either conversationally or by directly inputting G-code at the machine controls, the latest machine being fitted with the Fanuc Series 0iMF Plus. Any particularly complex features are developed in Ansys SpaceClaim and imported.
Mr Hirst concluded, “We continue to buy Leadwell machines because they maintain their accuracy over decades. The oldest model we currently operate is more than 20 years old. Our operators like them too, as the machines do not cause any trouble and the Fanuc control option is also popular.
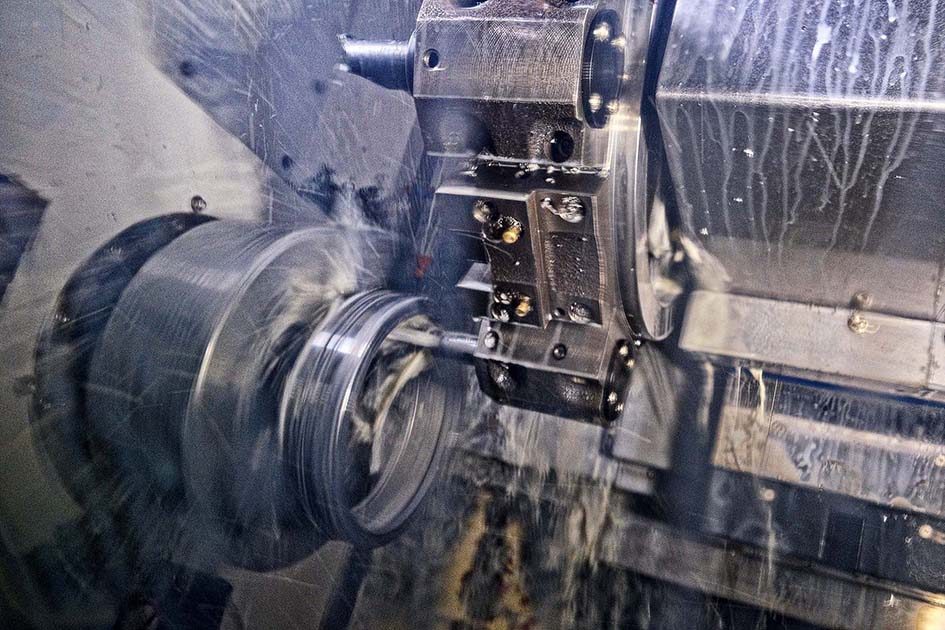
The LTC-25iL lathe in action.
“Over such a long period since we bought the first machine, it has been interesting for me to observe how Leadwell has progressed as a machine tool manufacturer on the international stage. Their mills and lathes were always good, but they are even better now.”