Sodick Europe is delighted to announce a new generation of high-precision EDM die sink machines: the AL40G and AL60G, incorporating the latest electrical discharge control technology, together with Artificial Intelligence functions and a precision thermal compensation system – as well as Sodick’s own market-leading linear motor technology.
In the 20 years since Sodick launched the world’s first linear motor driven EDM the company has shipped more than 50,000 such machines, which have won international recognition for their technical superiority.
The new die sinkers provide improved machining accuracy, speed and quality, from roughing and semi-finishing through to finishing, as a result of a range of new technologies including the latest EDM controls and electrical discharge circuits.
In addition, the machines benefit from a highly rigid structure, with temperature sensors installed throughout the machine body, to minimise the effect of temperature changes during high speed machining.
Large, easy-to-operate,19-inch touch panels come as standard, while the LN Professional Artificial Intelligence program ensures ideal machining conditions at all times, enabling the AL40G and AL60G to be operated optimally by both beginners and experts alike.
Ease of access is provided by the three-sided, automated, vertical drop machining tank, which enables the incorporation of a wide variety of automation technologies.
These machines are equipped on the XYZ axes with Sodick’s high-output linear motors, providing excellent machining performance and maintaining high accuracy over long periods of time. The linear motors are driven by the newly developed SP power supply which enables highly accurate positioning and also doubles servo responsiveness compared to conventional technology.
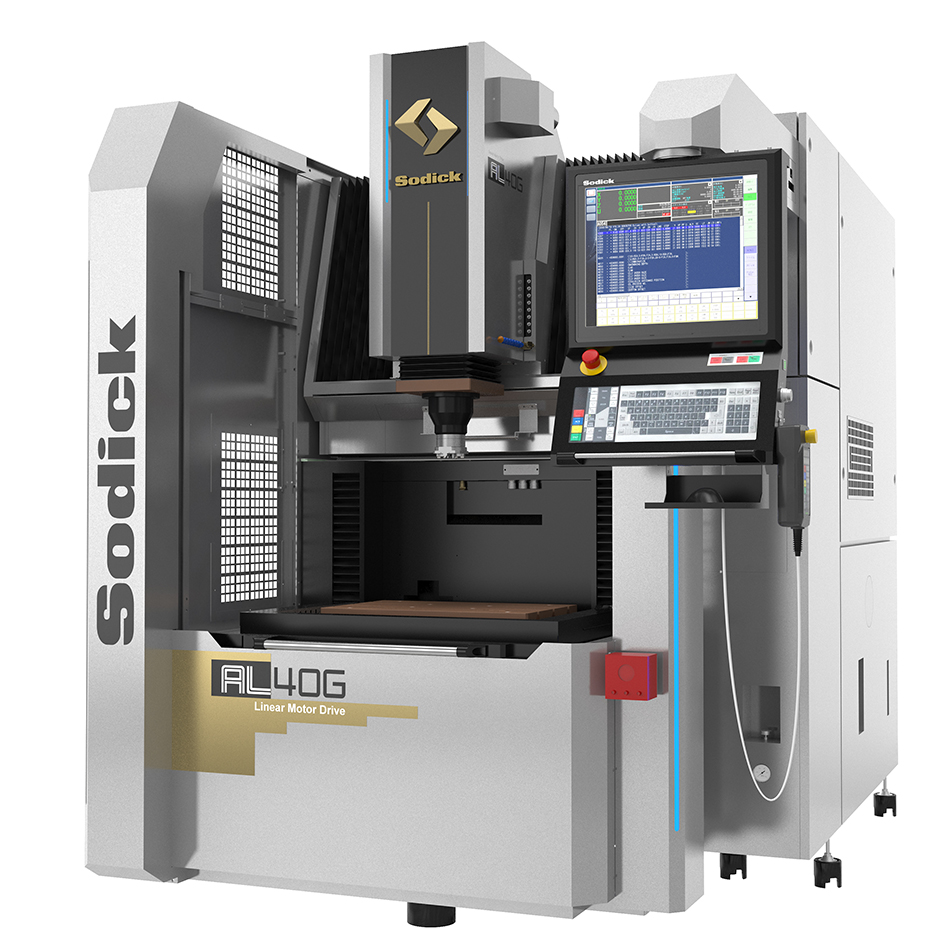
Sodick AL40G
The extremely rigid machine structure was optimally designed using state-of-the-art CAE analysis technology, while the incorporation of a new precision correction function, “TH COM”, minimises the effect of temperature changes within the machine, reducing the amount of thermal displacement by 50% compared to a conventional machine.
The new AL40G/AL60G series is equipped with Sodick’s independently developed lightweight, high rigidity ceramic sliders with low thermal displacement for the slide portion of the main spindle linear motor. The combined effect of this together with the high speed, dynamically responsive linear motor results in greatly improved straightness and a smooth drive, significantly contributing to increased speed and the stable machining of deep ribs. The high-speed jump effectively discharges machined tips, reducing abnormal arcs and the machining shape defects attributed to secondary discharge, thus greatly reducing the machining time.
One of the prime considerations in the design of the AL40G / AL60G was the development of an energy-saving, recycle/reuse, people-friendly, waste reduction and maintenance free eco-friendly machine tool – in-line with Sodick’s global policy of working to continuously improve its environmental impact ,which is central to the company’s development vision.
For further information visit www.sodi-techedm.co.uk / sales@sodi-techedm.co.uk