With the UK’s plastics industry turning over £23.5 billion each year and employing approximately 222,000 across 6,000 businesses, it’s no surprise that continued efforts are being made by industry figures to improve health and safety measures.
But with Brexit looming and an increased focus on sustainability, there are new challenges on the horizon. As new risks arise due to changing processes, organisations need to manage health and safety with the same degree of expertise and to the same standards as other core business activities.
Nigel Flowers, President of the Polymer Machinery Manufacturers and Distributors Association (PMMDA) and Managing Director of Sumitomo (SHI) Demag UK discusses how industry is driving improvements in processing to help overcome these challenges and the impact of new safety standards guidelines set to be released in the coming months.
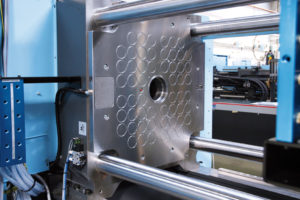
Ensuring the mould is secured correctly with the correct number of poles on a magnetic clamp system is vital for making the process safe
Safer systems
The plastics industry has an exceptional health and safety record, as demonstrated by BPF accident survey statistics[1]. However, no company can predict what is around the corner, notes Nigel.
In the case of service teams, although the engineers themselves are well trained and qualified, a group of machinery suppliers – Sumitomo included – found that potentially the most hazardous aspect of an assignment was getting to and from site. Contributing risk factors included long hours, driver fatigue and use of mobile phones in vehicles.
In a bid to eradicate these risks, the suppliers defined the Safe System of Work guidelines, which have been updated and will be released under the PMMDA umbrella this summer. In addition to outlining how best to deal with travel, the guidelines aim to help define who is responsible for the machine at any given time.
“The permit to work system is especially important, to avoid any ambiguity over who has control of the machine. For example, is it the customer or the service engineer? As a next step, we are planning to develop a common approach to Permit to Work schemes to make sure it is crystal clear who is in control,” comments Nigel.
Additional topics covered in the Safe System of Work guidelines include reporting procedures, risk control measures, the work at height regulations, and PPE. These are all tied together with the intention of producing a unified approach for the industry.
“There are risk assessments for every job, but the trouble is that everybody does it differently. What we want to try and have is a common approach,” explains Nigel. “Customers want risk assessments, method statements etc. The idea has been to try and produce a set of documents with the same content. This will hopefully make life a little easier for everyone involved.”
Brexit boom
New safety standards for injection moulding and injection mould clamping are under revision too, not only to address industry changes, but also to offset any complications posed by Brexit. “Once we leave the EU, there’s a high probability that we’ll need to maintain and develop our own British standards again,” explains Nigel. “We are in the process of converting the current BS:EN standards to the global ISO level, so that we can adopt those standards to UK law quite quickly should we need to.”
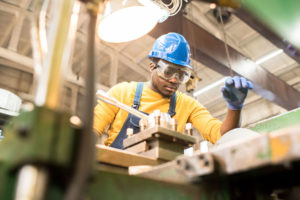
A common Permit to Work approach will help to clear up any ambiguity over who is control of injection moulding machines
The current machine safety standard BS:EN201 includes a description of interfaces to the magnetic mould clamping systems. Once this is replaced by the ISO:20430 standard, there won’t be any requirements for magnetic clamping systems, hence the need for a further ISO standard covering these systems.
“There tends to be a lot of misunderstandings about magnetic clamping,” adds Nigel. “The perception is that you can put any sized mould into the machine, but that’s not true. You can’t go too small, you have to make sure that the correct number of the poles are covered by the mould to ensure the mould is secured correctly. There’s a lot to think about and these are all areas to be addressed within a standard.”
Green future
Aside from the continual update of health and safety regulations under the Safety In Manufacturing Plastics initiative[2], the establishment of an environmental and operational safety management plan is now at the forefront of the plastic industry’s consciousness.
From pollution and carbon footprint to the UK ban on single-use plastic products, the industry’s role in the care of the planet has gained traction within the media and has led to a number of governmental actions. This includes a new tax from April 2022 for produced or imported plastic packaging that does not include at least 30 percent recycled content.
Rather than signalling the diminishment of the sector, organisations in the plastics industry are making corporate responsibility a priority. Nigel concludes: “Whether it’s LED lighting, variable speed pumps onto water systems, or electric injection moulding machines, there’s been a surge of investment in the reduction of energy consumption. A huge amount of work has been already done and that will definitely continue in 2019 and beyond.”