Initially founded to provide a service and rebuild facility for hot foil presses, which use heat to transfer adhesive-backed foil to imprint and personalise a wide range of goods from luxury handbags to bespoke stationery. However, it soon became clear to Karl and Ros French, founders of Metallic Elephant, that there was a strong market for high quality, British designed and manufactured presses and dies.
The development of its own range of hot foil presses began 5-6 years ago and has led to the Essex-based company fulfilling demand to many household brands around the globe, such as Samsonite, Next, Harrods, Burberry, Hackett, Prada and Tiffany. These businesses place the machines front-of house to provide customers with an instant and bespoke service. Demand is such that Metallic Elephant typically builds and delivers 350 presses along with associated dies and letter sets every year. Key to Metallic Elephants success has been its speed of response to customer orders for both machines and dies and the inherent quality that makes it proud to wear the Made in Britain badge, with some 99 per cent of the content of its machines being manufactured or sourced in the UK, allowing greater control of costs and reduced environmental impact due to logistics.
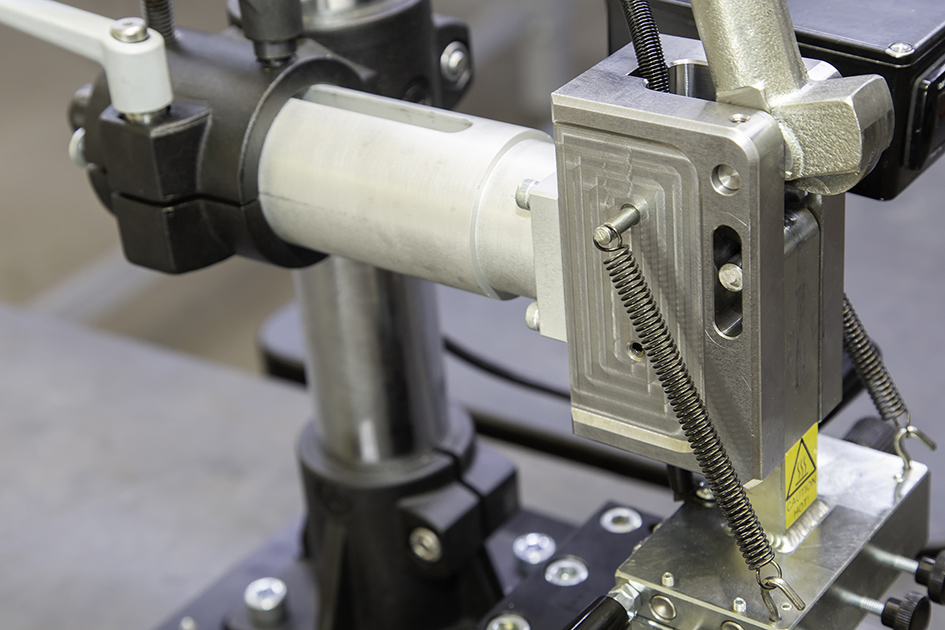
The two XYZ Machines at Metallic Elephant have helped improve quality and lead times allowing design and development of its latest KSF4 hot foil press (left) to be completed from start to finish in eight weeks.
“Quality is important along with our made in Britain approach and our success rate when we demonstrate a press to a customer in our showroom is a testament to that,” says Karl French. In the early days of manufacture many of the components for the presses were sourced from sub-contract suppliers, but with continuing strong growth, with 25 per cent year-on-year in the past four years alone, quality and lead-time issues began to surface and Metallic Elephant was drawn to the prospect of bringing machining in-house.
“Delays caused by quality and general late deliveries were beginning to impact on our ability to maintain deliveries, so we had to make changes,” says Wayne Mason, Metallic Elephant’s Manufacturing Manager. “The first step was our turning capacity and we replaced an old manual machine with an XYZ SLX ProtoTRAK controlled lathe. This addition made us realise the potential of CNC as the ProtoTRAK control was so straightforward and it certainly influenced our next purchase an XYZ 1000 LR vertical machining centre. The arrival of these two machines have given us control over manufacturing as we are now machining around 30 per cent of our parts in-house, a figure that will increase. As a result, we are also making things better and more efficiently, which in turn makes us more cost-effective and able to compete globally.”
The efficiency of having an in-house machining capability is highlighted by Karl French when discussing the latest addition to Metallic Elephant’s range, the KSF4 Hot Foil Press. “We completed every aspect of design and manufacture of this new product within eight weeks, start to finish including getting all of the CE and EN registrations done. All of the parts on this machine were manufactured in-house, with 90 per cent of them going on the new XYZ LR machine. Having this capability gives us the ability to amend designs quickly and get parts produced in one-off quantities were required very quickly. It all adds to our ability of being able to react quickly and give customers a next-day response on a lot of products. The investment in the XYZ machines has given us the confidence to push forward with our development and form part of our plans for further expansion of the business.”