During the 1980’s, the medical profession embraced titanium as the material of choice for implants that would be attached to bone.
Numerous studies presented titanium’s osseointegration* characteristics and further research highlighted the positive impact of textured, functional surfaces on osseointegration.
Compared to smooth “as-machined” surfaces, it was posited that texturing not only improves bone integration and thus implant stability; it also allows for the growth of supportive tissue and may even provide antibacterial advantages.
Today, the gold standard for titanium implants features such textured surface on all areas where integration with bone needs to take place. These functional textured surfaces are found on diverse devices such as bone plates, hip joints, and cervical and dental implants.
Additional research has been conducted in recent years into examining the relationship between the roughness of a surface and both osseointegration and vascularisation rates. Determining the optimum values for surface roughness for a given set of conditions is expected to remain an area of focus for several years to come.
Although in the past, roughness was mostly described by the two dimensional Ra Value (a measure of the variation in height), 3D measurements including the arithmetical mean height of the surface (Sa), texture aspect ratio (STr), interfacial area ratio (Sdr), core void volume (Vvc) and valley void volume (Vvv) are all now commonly used to describe a desired end result.
Production challenges
Textured surfaces traditionally have been achieved through the use of grit blasting (also known as sand-blasting) alone or in combination with chemical etching. Grit blasting in combination with acid etching is perhaps the most widely used approach adopted today.
The etching process involves using a strong acid – often hydrochloric, nitric, or sulphuric – to erode the surface area after blasting, resulting in microstructures from 1 to several microns in diameter. A neutralisation phase, in which the acid is reduced by the addition of a base or multiple washing cycles using de-ionised water, completes the process. Etching is both time- and temperature-sensitive, and requires the appropriate (safe) infrastructure to handle both dangerous chemicals and waste by-products.
Blasting is a mechanical process by which a hard particulate (sand, salt or ceramic) is projected at high velocity against the surface to be treated. Particle size, velocity, and impact angle all influence the final surface roughness.
Both blasting and etching result in a random distribution of surface features. Chemical changes to the outer layer of titanium can also occur. The choice of blast material as well as process parameters (time, angle, size and blast velocity) need to be developed based on the desired end result. Most often, the blast material is a single-use consumable and must be disposed of after part processing.
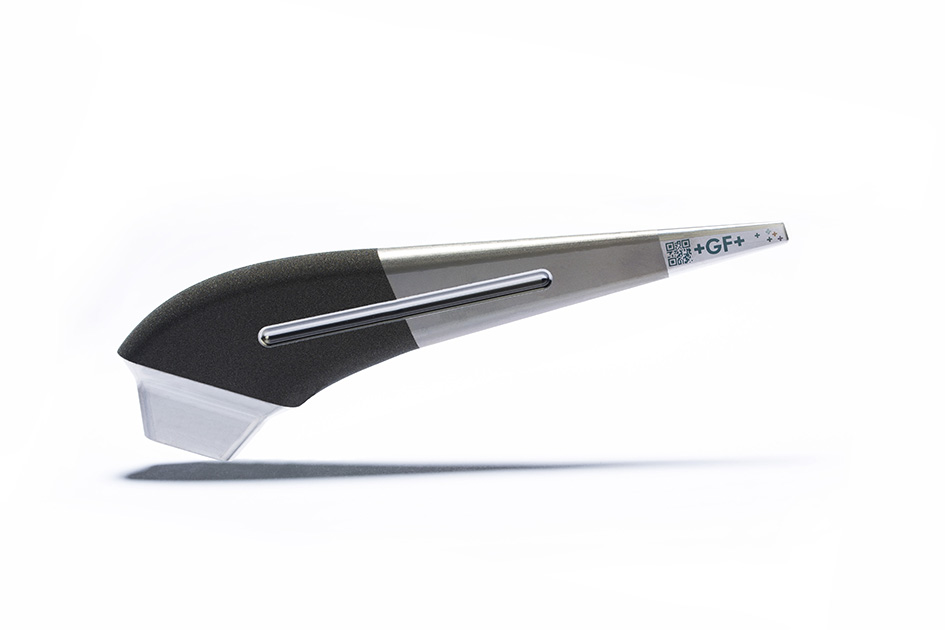
Example of a textured titanium implant.
Secondary processes introduce risk
Both blasting and chemical etching usually require manual intervention by operators in order to mask surfaces that are to remain untextured. Both also require the component to be cleaned after the texturing treatment. It is interesting to note that residue from blasting is difficult, if not impossible, to eliminate entirely.
Proper washing after blasting can be a multi-step process that adds time and requires specialised equipment such as tanks or ultrasonic wave technology.
An error in the washing (e.g., wrong or incorrectly dosed chemicals), or the handling process can affect product quality – leading to potential product failure and costly recalls.
Due to these issues, device manufacturers are looking for alternative ways to manufacture textured functional surfaces without secondary washing – and to gain design flexibility in terms of surface properties.
Laser texturing as a substitution to sand-blasting
Laser texturing replaces a random process (e.g., blasting, etching) with a digital one.
Pulses of laser light, often delivered in a nitrogen or argon shield gas environment, are directed at the materials’ surface. The laser heats and modifies the metal, creating local surface deformation. Pulse duration, measured in nano-, pico- or femtoseconds, is very short and the impact location and pattern are precisely controlled with an end result that:
- is repeatable (i.e. not dependent on operator judgement but programmed into the controller);
- is clean (i.e. no particulate is generated, and little or no chemical change occurs to the metal);
- does not use consumables such as blasting materials or acids, bases or washing systems;
- does not require secondary handling, part masking, or (in most cases) any secondary cleaning;
• does not require 100 percent final product inspection.
The use of laser texturing allows a surface to be structured/textured with a precise, repeatable pattern and enables both product designers and manufacturers to design in and meet more exacting specifications for roughness.
Multiple different textures can also be applied on the same device without any need for masking – and elements such as 2D bar codes or other unique device identification (UDI) features can be easily integrated.
Manufacturers concerned with counterfeiting can use proprietary textures, or can add logos or hidden patterns confirming the device origin – detectable even after many years of use. Recent research has also indicated that precisely controlled, laser-generated nano-structures may yield functional surfaces with specific antibacterial properties.
The choice of laser texturing technology (pulse duration, power, texturing pattern) will be driven by the desired surface that the manufacturer wants to produce.
Lasers that operate with a nano-pulse duration will both ionise metal and locally heat the surface being treated, resulting in a surface with an increased Sdr, Vvc and Vvv as compared to femto-second lasers.
Femtosecond pulses are much shorter and essentially eliminate the heat-affected zone (HAZ), resulting in a surface with lower variation. Both technologies are useful and the choice of which to use depends on the desired end result of the surface in question.
Most textured surfaces are not flat, but have complex, curved geometries. A key criterion in the quality of a laser texturing solution is the ability of the system to correctly compensate for these curved surfaces. Most commercially available systems introduce errors when applying a texture to a curved geometry.
However, GF Machining Solutions’ Laser texturing machine tools make use of advanced software to allow the texturing of even the most complex surfaces.
Conclusion
The use of texturing on functional surfaces in order to speed bone growth and provide other patient benefits is well documented.
Texturing can be achieved through various processes including blasting, chemical etching, and laser texturing. Blasting and etching, however, create a random surface and increase both cost and risk by requiring multiple part handling and cleaning operations, as well as use of consumables (e.g., blasting materials, acids) and infrastructure.
A functional surface that is produced using laser light and an appropriate shield gas under a digital process results in a repeatable, structured functional surface that is essentially identical for all parts being made.
In addition, laser texturing significantly reduces, or even eliminates the risk associated with masking non-textured surfaces and secondary cleaning. The ability of a laser texturing solution to correctly adapt textures to curved surfaces is also a specific strength and a clear differentiator.
Improved part quality, increased product differentiation, the ability to customise patterns (and more easily identify counterfeit products), a reduced risk of contamination, and reduced production costs and time – are all benefits that manufacturers can derive from laser texturing.
As the market leader in implant manufacturing technologies including Laser texturing solutions, GF Machining Solutions is uniquely positioned to support device designers and manufacturers as this technology becomes more widely adopted within the medical device industry.