EMO Hannover 2019 will show how smart technologies meet the production requirements of electro-mobility
The mobility concept for individual transportation will in the relatively near future be a combination of progressively downsized internal combustion engines and electric drives, say some, while others predict that electro-mobility will secure jobs or even create new ones. This, at least, is certain: traditional metal-cutting machines are a long way from being ripe for the scrap heap – equipped with smart technologies, they will also play a prominent role at the EMO Hannover 2019.
“Changing over to electro-mobility signifies a radical transformation of production technology,” the then President of the Fraunhofer Society, Prof. Hans-Jörg Bullinger, warned back in 2010. For example, he predicted, the entire value added chain will alter in the automaking sector. The importance of electrification for value creation in the drive chain was scrutinised in last year’s VDMA study on “Transformation of Powertrains”. It was authored by the Aachen-based company FEV Consulting GmbH, which specialises in the automotive and aviation industries. It forecasts that the increasing dynamism in the electrification of vehicles and in drive technology will lead to radical changes in Germany’s entire mobility and vehicle industries and in significant parts of the mechanical engineering sector. Moreover, a vitally crucial role will be played by the research community and cross-sectoral networks.
Though the FEV’s experts anticipate that sales of internal combustion engines (including hybrid drives) for passenger cars in Europe, the USA and China, the three markets examined, will fall by ten per cent by 2030 compared to 2016, nonetheless, substantial business will remain for component manufacturers, plus machinery and line producers. Because improved drive technologies – e.g. efficiency-boosting measures in the internal combustion engine and the transmission – also entail more stringent requirements for the production technology involved.
At the same time, the study’s authors are anticipating a share of 22 per cent in these three markets for exclusively electro-powered vehicles. The effects of electrification on the individual production processes that dominate for conventional drives are substantial. With a battery-electric drive, for instance, their value added is reduced by an average of 64 per cent (excluding battery cell production). For (plug-in) hybrid drives, by contrast, value added will rise by 24 per cent – here, besides an internal combustion engine an electric drive is also installed.
What’s crucial here is the bottom line. There, the study shows that the combination of hybrid drives, a higher level of complexity at the internal combustion engine, and rising sales figures for vehicles (particularly in China) will exert a beneficial effect overall on the amount of value added.
In the estimation of the VDMA’s President Carl Martin Welcker, “the mobility transmutation process means enhanced opportunities for additional value creation in the mechanical engineering sector – for us, “transformation of powertrains” can be a source of growth”. There is still time for the companies, he continues, to master the transformation successfully, in order to modify business models and technologies appropriately. At the same time, however, the study shows clearly that “hybridisation and electrification will gain wide acceptance on the market.”
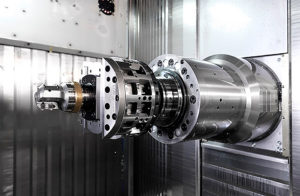
The new CBC (Cylinder-Bore-Coating) process technology as a constituent of automated production lines for crankcases.
Mechanical engineering sector benefits from electro-mobility
The opinion of the VDMA’s President is shared in full by Marc Kirchhoff, Head of Industry Management Automotive at Trumpf GmbH + Co. KG in Ditzingen: “Plant and machinery manufacturers in Germany can benefit from electro-mobility.” The mobility of the future will at Trumpf at the very least secure jobs in R&D, production and applications engineering, and in some cases create new ones, “since lasers are indispensable for competitive production of electric cars. And today we’re already seeing a rising level of demand for production technologies involving electro-mobility.”
Due not least to the “equal attractiveness of internal-combustion and electric vehicles” forecast for 2024, says the VDMA’s President, the process of transformation should be tackled now at the latest by the companies concerned. That, says Marc Kirchhoff, “is precisely what we’re doing, and on different levels. With our knowledge of the sector and the applications involved, for instance, we’re already supporting the sector in comprehending and developing new technologies and setting up complete production lines for series manufacturing. Many component suppliers and automotive specialists ask us to help in changing over their production operations for electro-mobility, because we’re familiar with the requirements nowadays faced by electric car manufacturers and their component suppliers, not least from other sectors.”
Many of the company’s existing products can “be used as they are for manufacturing electrical components”. For example, more than 500 lasers have been sold worldwide for use in battery production alone – and the number is rising steeply. “Our technologies are in widespread use among battery manufacturers,” reports Marc Kirchhoff. “At Trumpf, one euro in ten of automotive sales is already accounted for by battery manufacturing.”
Marc Kirchhoff explains the effects of electrification on the company’s individual production processes like this: “In our order books, we are seeing a significant rise in focusing lenses in conjunction with high-performance lasers for ultra-productive lines in the field of electro-mobility.” This is complemented by progressively more inquiries for green lasers used for welding copper and for solutions for cutting carbon-fibre-reinforced plastics. It can thus be concluded that many firms in the automotive industry and its component suppliers, but also some new players on the market, have recognised the signs of the times and are preparing their production halls for mass manufacturing of electric cars. And because these inquiries are rising so significantly, “we offer lasers and laser systems specifically for the requirements of electro-mobility”.
Proportion of metal-cutting set to remain steady in the medium term
“The individual-mobility concept of the near future will be a combination of progressively smaller internal combustion engines and electric drives,” believes Manfred Maier, Managing Director and COO (Chief Operations Officer) of the Heller Group, Nürtingen. There are numerous indications that the politically postulated goal of fully electrified vehicles cannot be created overnight; this will involve a protracted process featuring numerous intermediate steps: “For example, it’s probably going to take years, perhaps even decades, to put in place a fit-for-purpose infrastructure.”
Currently, at least, all relevant studies concur in predicting that passenger car fleets worldwide will increase by another 30 million vehicles over the next ten years. Purely electric vehicles are forecast to account for hardly more than ten per cent of this figure. In the upcoming ten, twenty or more years, says Manfred Maier, “internal combustion engines will accordingly remain the paramount drive concept. For us, this means that in the medium term the proportion of metal-cutting work will tend to increase and as time goes by will not significantly decrease – if at all.”
In response to the call by the VDMA’s President to tackle with promptitude the process of transformation in the companies, Heller’s COO Manfred Maier has a differentiated opinion: “First of all, we should realise what’s actually involved here. The paramount focus is on global CO2 emissions. This involves much more than just the questions of what drive concept a car is powered by or how a city’s air quality can be improved.”
This is why for years now, he continues, Heller has been productively engaged not only with the cutting of blocks, heads, crankshafts and transmission housings. The product spectrum primarily comprises four- and five-axis machining centres, plus milling and lathing centres for meeting the multifaceted requirements of the general mechanical engineering sector, the aerospace industry, energy engineering, contract production, and many other sectors.
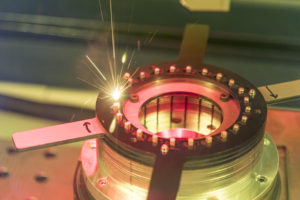
Lasers are indispensable for competitive production
of electric cars. In an electric motor, the magnetic
stator, particularly, requires a high production
outlay.
In addition, Heller has also adapted to the new situation in terms of its corporate structure. The Development New Business & Technologies Department addresses issues that will not immediately and directly become major earners, but may be important in the more distant future. Specialists there address the possibilities of additive manufacturing and new materials like CFCs.
The CBC (Cylinder-Bore-Coating) technology implemented exclusively in Heller’s machining modules, explains Manfred Maier, “is an excellent example of innovative technology supplementing the existing comprehensive machine portfolio. And it makes a significant contribution towards reducing CO2 emissions.” In 2016, the CBC technology was even nominated for the German Future Prize. The CBC cylinder bore coating process is based on the LDS two-wire technology used by Daimler and BMW, and is “so far the only one that can be reliably used for a relatively high production volume”. Around one million four- and six-cylinder engines will be produced with it per annum at Daimler in Untertürkheim alone. And since the end of 2018, a total of 65 coating lines for over eight million motors have been up and running worldwide.
EMO Hannover as a platform for solutions of the future
Heller’s COO Manfred Maier summarises his expectations of the world’s premier trade fair for the metalworking sector as follows: “The EMO Hannover 2019 offers us a platform for talking to our customers about current and future manufacturing requirements and finding shared solutions. The EMO is at the same time also an excellent indicator for identifying developments in technologies and processes, and in machine tool manufacturing, and at our customers as well, and possibly deriving from them new business models.”