Long-term partnerships build success
In a relatively short space of time Complete Engineering Services (Carlisle) Limited has grown into a successful sub-contract design and sub-contract manufacturing business, with expertise in machining, wire erosion, welding and assembly. Initially located in an old silage pit the two co-founders and joint managing directors Alan Walker and Andrew Monkhouse began working part-time in the business. As their reputation grew, and additional staff were recruited further expansion was necessary and the business was formally incorporated in 2003 when the two directors became full-time employees themselves.
“We were just two guys who had this crazy idea that we could make this engineering lark work for us. We rented the silage pit and built walls around it for our first home, which is still part of our factory to this day,” says Alan Walker. “Our work mainly came through word of mouth and we gradually added people and machinery to the business, employing our first apprentice as early as 2002. Part of our success as we celebrate 20 years in business have been the partnerships we have developed with customers and suppliers such as WNT. Continuity of people is important to us and over our first 20 years we’ve established lots of relationships. We’ve worked with WNT for 14 years and to be able to phone up or when Matt, the area technical sales engineer, makes his fortnightly visit to look at ongoing work and know things will be sorted is a nice position to be in.”
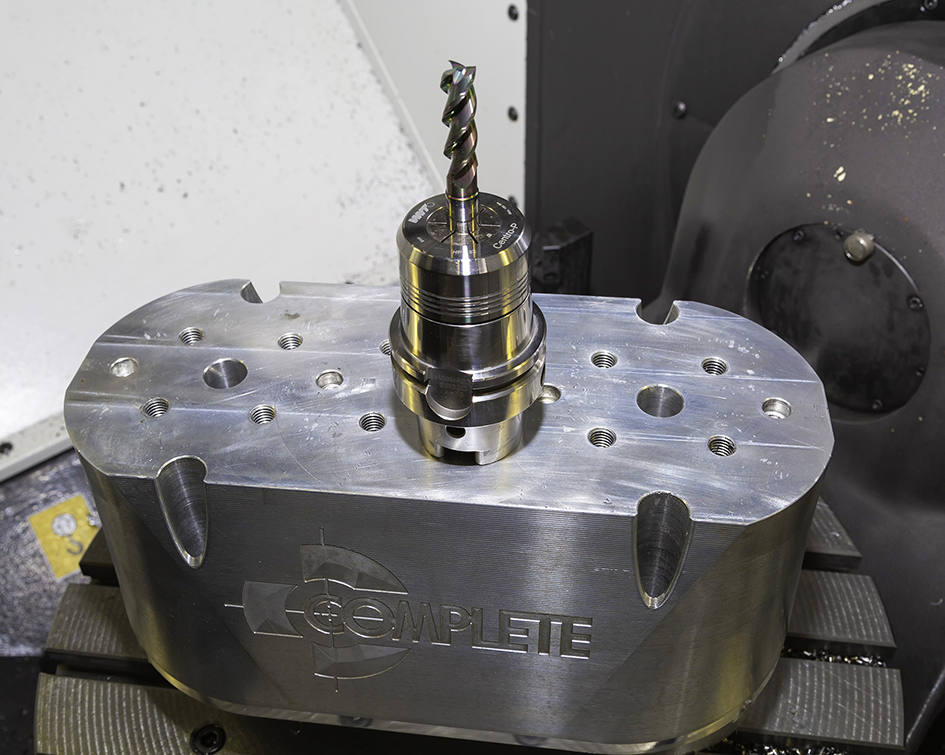
The WNT DLC cutters are used extensively at Complete Engineering Services
Initial growth at the company was steady, taking on its first employee apprentice in 2001 (the company has had 11 apprentices, many still working for it). Then a call from their ex-employer asking if they could take on a major project to transfer a production line to Italy allowed them to develop at a faster pace. “The contract to move this line was a major opportunity and the finance from that allowed us to increase investment within the business and expand our machining capacity. This meant a greater reliance on our tooling suppliers including WNT,” says Andrew Monkhouse. “With WNT we know we will get a quick response and it will be the right response, whether we are on the telephone or face-to-face with Matt Darbyshire, our area Technical Sales Engineer we are confident that the information we get is good and will lead to improvements in productivity.”
With an extensive machine shop that includes turning centres, 3- 4- and 5-axis machining centres, along with wire erosion and welding capabilities Complete Engineering Services draws in work from a wide spectrum of customers, from motorsport, through automotive, agricultural equipment and food processing companies. Therefore, there is always something new to look at. Most recently investment in a Mikron five-axis machining centre drew on WNT’s experience for a total work holding and tooling package. Working with Matt and WNT’s Applications Engineer Billy Poore, a total solution was delivered including assistance with post processing of programs and the supply of CAD drawings of vices and tooling.

WNT’s Work holding solutions include the ZSG series of vices, Zero Point clamping and the Alu-Form Collets
The work holding package was a combination of WNT’s ZSG4 Zero Point vices, MNG Zero Point plates and riser blocks and a collection of MNG Alu-Form collets. The latter is a machinable collet chuck for second operation work which allows the company to machine a form into the collet for precise gripping of components with irregular shapes. Once the batch has been completed the collet can be skimmed ready for another form to be machined. “To remain competitive we have to keep investing in tooling as the market is developing so quickly and, we endeavour to push everything as hard as we can to maximise productivity. A part of our philosophy is not to compromise, so we buy tooling specifically for each job, then we know we have the right tooling. While this may sound extravagant, it is fully justified by the productivity gains that we can make,” says Andrew Monkhouse.
Other examples of maximising tooling performance can be seen in the use of WNT’s DLC (Diamond Like Coating) end mills for machining aluminium and the WNT 2011 face-mill system where Complete Engineering are running it with a 2.5 mm depth of cut, 60 per cent stepover with speeds and feed of 300 m/min and 0.5mm/tooth. “Our business with Complete Engineering Services has grown in line with their business and is all down to the relationship that we have developed. We were willing to stand on the duckboard when they were a much smaller company and that commitment has been rewarded in this long-term partnership,” says Matt Darbyshire, Technical Sales Engineer, WNT.
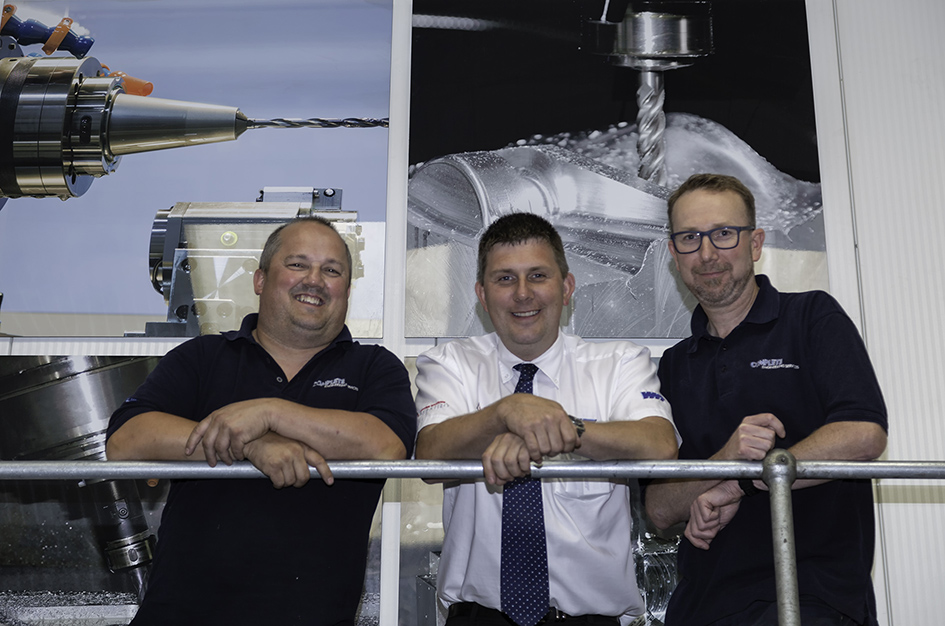
L-R Andrew Monkhouse, Matt Darbyshire and Alan Walker
Of course, partnerships are a two-way street and involve more than just ‘business’. Both Alan and Andrew have experienced WNT’s hospitality in the form golf and shooting and, are regulars at the WNT/XYZ Machine Tools Trackday hosted by Moto3 racer Sam Burman, who is sponsored by WNT. “At the last trackday we had the idea of paying something back,” says Alan. “As Sam is a machinist herself we were happy to offer to sponsor her racing helmets, something she was very pleased about. In return she paid us a visit on her way to race at Knockhill in Scotland, spending several hours talking to all out guys, who were fascinated by her story. This is just a small way in which we can return some of the benefit that we’ve had from our partnership with WNT over the years and a nice way to help celebrate our 20th Anniversary.”