Formed in 2013 when Lee Coles bought out a one-man machining business, Weymouth-based LC Precision Engineering has achieved sales growth in excess of 600 per cent over the past five years. Working across a variety of industry sectors, including defence, motorsport, nuclear and electronics, mainly focussing on work that could be produced on its three-, four- and five-axis vertical machining centres. To further develop its offering the company has now invested in new turning capacity in the form of an XYZ SLX 1630 ProTURN lathe.
With five employees including Managing Director Lee Coles, LC Precision Engineering may be a small business, but it has big ambitions, it is one of the first companies to transfer from ISO9001:2008 to the latest ISO9001:2015 quality standard and is currently implementing AS9100 Rev D for the aerospace sector. “This has been an exciting five-year period for the business, we have seen this growth develop through word of mouth on the strength of our reputation for quality and also a willingness to invest, which as seen over £175,000 being spent on new equipment in the past two years,” says Lee Coles.
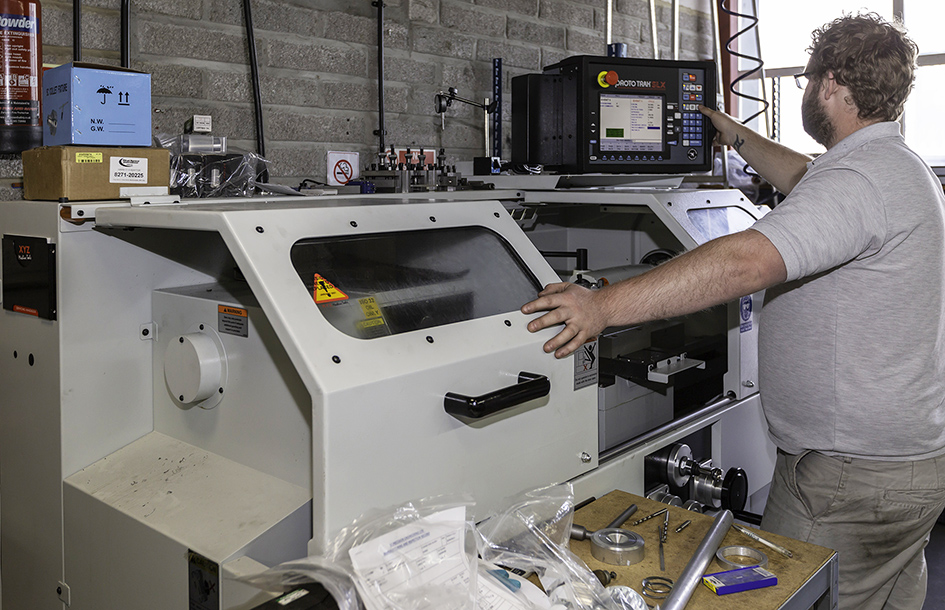
Lee Coles found programming the SLX 1630 ProTURN lathe straightforward.
The latest arrival is an XYZ SLX 1630 ProTURN lathe described by Lee Coles as being ‘in a different league’ when compared to his previous experience on manual lathes. While the SLX 1630 may be the entry point for ProTURN lathes it comes with an impressive specification from its cast bed and base, which provides a solid platform through to the 400 mm swing over the bed, 760 mm distance between centres and a versatile 5.75 kW, 150 – 2500 revs/min constant surface speed spindle. The machine also comes with three-jaw chuck, quick change toolpost and interlocked guards for when running in CNC mode through the ProtoTRAK control.
The SLX ProtoTRAK was key in the decision by Lee Coles to go with XYZ Machine Tools for his move into CNC turning: “The control system definitely sold the machine to us. We specialise in lower volume work with seven out of ten jobs we do being one-offs, and our reputation is built on working with customers in prototype development through to production, where we can add our input to design and help to reduce costs for customers. Therefore, the ability to easily programme complex forms and be confident that we will achieve a good part first time, every time, thanks to features like TRAKing and Do-One on the ProtoTRAK control makes a huge difference.”
The TRAKing feature is standard on all ProTURN lathes and allows an operator to use the machine’s handwheels to move the machine through the program. The faster you wind the faster the machine goes, and you also have the ability to stop and rewind if required. Once happy the operator switches from TRAKing to CNC Run and the machine takes over the process. Likewise, the Do-One feature simplifies manual machine operation by assisting the operator in creating features such as radii, tapers and fillets in combination with the electronic handwheels. A major timesaver on one-off and prototype work. The simplicity of the control meant that the machine was producing parts the day after it was commissioned, with one operator undergoing a day’s training at XYZ and Lee able to learn the system simply by using it.
“This has been an extremely positive purchase for us, it is already opening up new opportunities for work from existing and potential new customers, and it is definitely work we could not have won without the versatility of the ProtoTRAK control, and it won’t be our last XYZ lathe.” says Lee Coles.