A second pair of twin-pallet, horizontal machining centres (HMCs) from Heller has been installed in the Booth Drive, Wellingborough factory of Mahle Powertrain, an independent company specialising in the design, development, test and manufacture of combustion engines. A 4-axis Heller H2000 has joined two identical models in an eight-machine production line dedicated to manufacturing cylinder blocks, while a larger, 5-axis FP6000 has been added to a flexible machining cell to expand its capabilities.
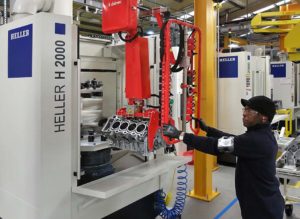
Dalmec equipment is used for handling the aluminium cylinder blocks in and out of the Heller H2000 machines.
At the end of 2016, Mahle’s project manager Geoff Brown, production engineer Bob Price and others decided that the decade-old line producing aluminium engine blocks for a major British OEM needed to be upgraded. It comprises six HMCs each performing separate operations plus two bore honing machines positioned at the end.
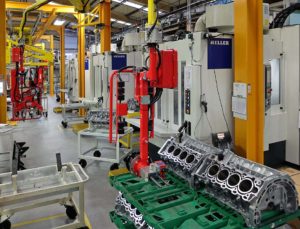
A view from the other end of the three Heller H2000 HMCs.
All HMCs were originally supplied by a Japanese manufacturer, but in early 2017 the first two machines in the line were replaced with Heller H2000s. Designed at the company’s German headquarters, they were manufactured at the group’s UK factory in Redditch.
Mr Brown advised, “We were already familiar with Heller machines, as we operated 21 of them very successfully for more than a decade at our facility in nearby Ryle Drive.
“They were used for manufacturing cylinder heads and blocks for a British off-road plant manufacturer, although that contract has now ended and the machines have been sold.
“I also had experience working with Heller horizontal machining centres at another engine manufacturer that operated more than 20 of them in a transfer line.
“We sent some V8 cylinder blocks to Heller’s Redditch technical centre, where they carried out Op 10 and Op 20 trials on an H2000, which is ideally sized for the work.
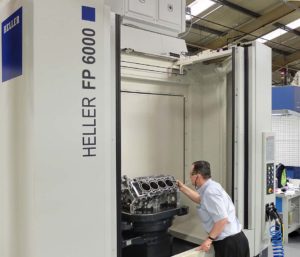
The Heller FP 6000 5-axis HMC has been added to a pre-existing flexible machining line that already comprised a vertical machining centre and three HMCs of a different make, all 5-axis models, at Mahle Powertrain’s Booth Drive factory.
“Op 20 was particularly successful, as with new fixturing it overcame a problem we were having machining a side port in the new model of cylinder block currently in production.”
Consequently, the first two machines in the production line at Booth Drive were replaced with Hellers and the benefits were immediately noticeable. Mr Price advised, “The cycle time for each of the first two operations is one-third faster on the new machines, eight minutes instead of the previous 12.
“Impressively, the 33 percent time reductions have been achieved despite adding extra routines by including some sections of the Op 40 cycle into Op 10 and parts of Op 30 into Op 20.”
The raised productivity is largely down to the rigidity of the H2000s, the higher speed (16,000 rpm) spindles with HSK63A interface and programmable through-coolant up to 70 bar, all of which allow faster cutting feed rates. Rapid traverse is quicker than before and further time savings derive from integral hydraulics for automatically clamping the engine blocks and air detect for checking that the component is seated correctly. A probe in the tool magazine for identifying broken cutters shaves off further time by removing that function from the cycles.
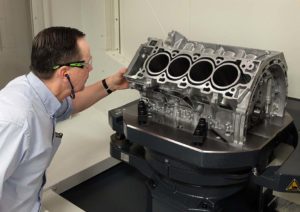
Mahle Powertrain project manager Geoff Brown inspecting a cylinder block machined on the Heller FP 6000 5-axis HMC.
Mr Brown pointed out that all these features are fitted as a matter of course to the Hellers, whereas many other machine manufacturers class them as extras, increasing both cost and delivery lead-time. The offer of generously equipped, standard machines, with the enhanced back-up that their manufacture in the UK promised, was a significant factor in Mahle’s choice of the H2000s to upgrade the line. So also was the efficient swarf management, essential to remove large amounts of aluminium chips efficiently from the machining area and avoid hours of costly machine stoppage to clear accumulated swarf.