Advanced Grinding Solutions (AGS) has booked one of its biggest ever stands at the forthcoming Mach show where it will be exhibiting six machines. None of these machines have been exhibited here before and therefore many UK engineers will be getting their first opportunity to see this range of advanced grinding and finishing machinery; the widest range on display at the Mach show.
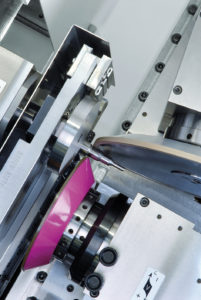
Rollomatic NP5 Machine
Rollomatic, a leading Tool Grinding machine manufacturer, is demonstrating its intention to increase its market presence here by exhibiting its NP5 ShapeSmart machine in the UK for the first time. This machine is used by many UK cutting tool manufacturers to quickly and easily cylindrically grind carbide and HSS tool blanks to diameter and form shape rather than to do so on multi-axis tool grinders whereby the blank preparation process on those machines takes considerably longer, is more expensive and is generally not as accurate. Cutting tool and punch manufacturers are invited to receive a demonstration on the many advantages of the Rollomatic NP5 and to understand more about Rollomatic’s wide range of CNC tool grinding machines.
The Rollomatic machine is suitable for the grinding of components up to 25mm in diameter and has an integrated robot loader with a capacity for up to 1,000 parts. The NP5 grinds to mirror finishes, can control diameter size to +/- 0.0005mm, and runout concentricity within 0.001mm. Fast cycle times are assured due to Rollomatic’s patented “Pinch & Peel” grinding process whereby the machine has the ability to mix a multi-pass rough grinding operation with a final through-feed pinch grinding pass and, if required, rough and finish grinding in a single pass. The NP5 machine is also able to grind non-round special forms and flats as required for punch tools. This is the first time that Rollomatic has exhibited a grinding machine here in the UK.
Rollomatic’s line up is completed with their LaserSmart 501 machine that features the simultaneous 5-axis high precision laser machining of tools made from ultra-hard materials such as PCD, CVD, and natural diamond. The LaserSmart 501 processes multiple operations such as cutting-edge generation, chip breaker machining and cylindrical land machining in one complete set-up and can produce cutting edges with a radius of under 1um.
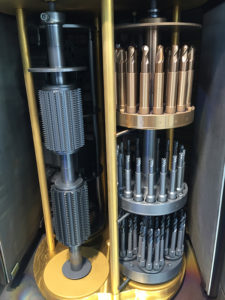
Various tools on Platit Coating machine
Platit are also exhibiting in the UK for the first time exhibiting their latest Pi111 Plus coating machine; the first time that any coating machine of this type has been shown at a UK exhibition. The Platit machine being demonstrated will be supported by the presence of Dr Tibor Cselle who is one of the world’s foremost experts on coatings for cutting tools and will be exploring topics such as why tool manufacturers should invest in their own coating technology and what are the latest and best coatings for various milling and drilling applications.
The main application for Platit coating machines is the coating (usually TiN, TiCN, CrTin, etc) of end mills, form tools, drills, inserts, saw blades, and broaches. Platit offers cost effective solutions in order that tool manufacturers can coat their own tools instead of relying upon expensive subcontractors. Tool manufacturers that are driven to produce tools that last longer and cut faster also need to differentiate their products from their competitors and coating offers them the ability to do this. Cost saving is only one driver for a tool manufacturer to invest in a Platit coating machine; another important reason is to reduce the time from order to a finished product because no external sub-contractor for coating tools can respond as fast as an in-house facility. Platit do much more than manufacture coating machines; they are constantly developing new coatings for their customers and offer a full consultancy service for their end users to ensure that they are using the optimum coating for their applications.
Magnetfinish machines for cutting tools use a unique process that’s been developed to dramatically increase the performance and lifetime of tools which last much longer and can be ran at higher speeds and feeds after being processed using Magnetfinish technology. Abrasive powder is processed by magnets across the surface of cutters with controlled but variable directions. The ground surfaces of cutting tools are polished and the cutting edges are machined with a precisely defined and fully reproducible radius of between 3um and 50um.
Magnetfinish will be displaying their latest MF73 machine with 2 robots that includes for automatic loading from pallets – combined with wash, dry and demag. This allows entire batches of tools to be processed automatically without any operator involvement.
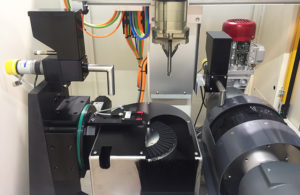
Magnetfinish machine for cutting tools
The processing times for cutting tools are extremely fast with the average machining time for smaller tools being in the region of 10 seconds.
High quality tools need perfect cutting edges. The accuracy of the radius has to be extremely tight so that a high or low flute does not cause uneven metal removal, thus affecting part geometry, surface quality and cutting tool life. The cutting edges of the flutes must have no jagged edges, chips, cracks or other irregularities. The presence of these would mean that the cutter edges would be subject to early wear as soon as they contact the workpiece for the first time and would lead to a rougher surface finish being created and a shortened tool life. This is the first time that cutting tool manufacturers will be able to see a Magnetfinish machine here in the UK.
Tschudin exhibits its new proLine CNC Centerless Grinding machine that receives its UK debut and, like other machines within the Tschudin range, benefits from a unique axis arrangement that sees the workrest blade being mounted onto its own CNC axis. This allows components to be loaded to the centerless grinding machine outside of the working zone of the machine. This feature is highly attractive for those looking to meet health & safety obligations because otherwise the hand loading of parts to centerless grinding machines can be dangerous.
The Tschudin proLine machine additionally features a world-first and patented 4th CNC axis to automatically move the regulating wheel vertically in order to eliminate the need to adjust the workrest blade height to keep part geometry consistent throughout the entire grinding process. Thus, operators no longer need to worry about wheel wear and to manually adjust to compensate for that and similarly when changing to a new workpiece the part programme can be recalled along with the optimum pre-selected and pre-defined grinding point and the regulating wheel will position itself automatically. This is an important advantage as it allows for much faster set-up times and also for millions of parts across multiple batches to be machined to the same pre-defined condition without the need for operator input.
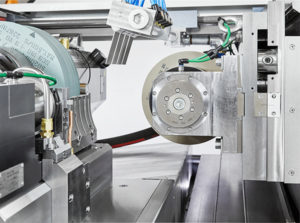
Tschudine proLine Grinding
The Tschudin proLine centerless grinder will plunge grind parts with a length of up to 280mm and with diameters from 0.1mm up to 180mm. It has a 410mm diameter grinding wheel and weighs 10,000Kg with its bed and spindle blocks made from natural solid granite.
FLP (Fine Grinding, Lapping and Polishing Machines) also exhibit in the UK for the first time. The broad range of FLP machines include both twin wheel – double sided CNC Lapping Machines and also single sided Lapping machines. Visitors to the AGS stand will see a relevant single sided machine from the latest FLP range with engineers invited to attend to discuss their requirements for the face machining of components.
FLP Double Disc or twin wheel machines have 7 machines in the range offering a working disc diameter of between 540 and 1,300mm. These are fitted with Siemens PLC controls, can all be offered with full automation via linear or robotic solutions, and weigh between 7 and 16 tons. These advanced machines are offered as high-precision versions with granite machine beds and the latest machine controls, drives and measurement technology. FLPs machines are in use across many branches of engineering including automotive, aerospace, bearings, optics and ceramics. Applications include the production of pump, bearing seals, fuel injection and transmission components. FLP machines ensure that components are produced to the closest possible tolerances and at the highest production rates. Operator friendly simple machine operation is ensured as is the lowest cost per machined component. FLP also manufacture in excess of 15 million parts a year for customers needing a sub-contract facility. This comprises flat honing, fine grinding, lapping, polishing and deburring of components including full process documentation, measurements and statistics. FLP will be exhibiting in the UK for the first time.
Automation is now one of the most important topics for all manufacturers due to the need to fully automate production cells to remain competitive. The Handlingtech range of loaders is suitably comprehensive with Fanuc or Staubli robots being used for handling parts from 1g up to 700 Kg. These are very versatile systems and are suited for loading a variety of machines. Various component storage solutions are available including the use of pallets, bowl feeders and conveyors. Siemens controls are used with software links to the donor machines own control system for seamless handling tasks. In order to “add value” to the loading equipment it is common for Handlingtech to incorporate other processes within their loaders such as automated measuring and checking via a variety of gauges and cameras and also automatic washing, cleaning, drying, deburring, assembly, laser marking and packing.
Chris Boraston of AGS comments; “Most of the machines that we sell into the UK are automated and as each year passes it’s clear that the need to automate increases further. This combined with the need for loaders to incorporate other technologies such as washing, deburring, measuring or assembly, has meant that today loaders have become machines in their own right and it’s now not uncommon for the loaders that we sell to do more, and therefore be more complex, than the actual machines that they service. It’s all about adding value to the load/unload process to reduce manufacturing costs and to reduce work in progress”.
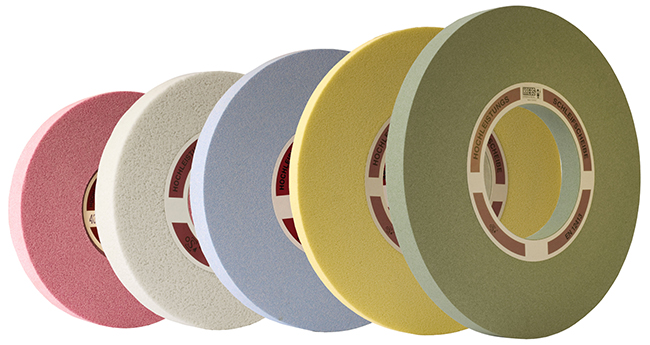
Krebs Multo Grinding Wheels
Specialists from Krebs & Riedel will be present on the AGS stand to discuss all grinding applications and best use of their range of internal and external grinding wheels. Krebs & Riedel manufacture high quality conventional, diamond and CBN abrasives and are constantly introducing new types of wheels with improved grain structures and novel bonding systems that enhance grinding wheel quality and optimise performance. Companies involved in grinding are invited to meet the Krebs & Riedel specialists and to discuss their grinding issues and aims to improve their grinding processes.
Apart from offering high stock removal rates to improve cycle times, combined with more consistent part quality by avoiding micro-cracks in the surface of sensitive parts, another large benefit of using Krebs wheels lies in large cost savings made possible by reducing wheel dressing requirements. This has the three major advantages of lower wheel waste due to less dressing, faster cycle times as wheels can be kept grinding longer in between dressing them, and also a reduced spend on expensive diamond rollers.
Krebs and Riedel are developing new wheels all the time and those are added to the existing collection of over 60,000 different wheel types that are available from them. With such a huge variety of wheels then of course choosing the correct and most efficient wheel is no easy task but customers can draw upon the experience of Krebs application engineers to arrive at the best one for the customer’s specific application.
The range of grinding and finishing machinery receiving its UK debut can all be seen on the AGS stand H20-960 at Mach.
For further information please see www.www.advancedgrindingsolutions.co.uk
or contact AGS on 02476 22 66 11