Describing itself as a one-stop-shop providing logistics, design, machining, and part finishing for a high profile list of customers in the aerospace sector, Nasmyth Arden is focussed on attention to detail and driven to reducing process times through improved machine efficiency. This has seen the company invest in new machining capacity as well as seeing benefits from environmental improvements.
Specialising in the machining of billet material, on its 30, three-, four-, and five-axis machining centres where up to 90 per cent of the original material may be removed poses its own problems, in terms of airborne oil mist and other particulates. As a result Nasmyth Arden is currently retrofitting every machine in its factory with oil mist extractor units from Matchmaker CNC. “Any new machine we buy will be equipped with the Matchmaker extractor system and we have started to add them to our existing machines, starting with the five-axis machining centres. The high speed nature of these machines generate heat and as a result oil mist. When a cycle has finished the operator used to have to wait until this settled within the machine before opening the doors, this wait is eliminated with the addition of the extractor units,” says Nasmyth Arden’s Production Manager Alan Lucas.
“Matchmaker CNC have been working with us for many years providing service and breakdown cover on a wide range of machines and when they introduced their range of extractors we could see the benefits they would bring and also that they provided a very cost-effective solution, allowing to quickly adapt them to all of our machines.” Key to the success of the Matchmaker oil mist extractor is its patented conical filter. This requires much less maintenance than existing systems with the added benefit of a filter life of up to five years, depending on application. The system is also highly efficient at particulate capture removing up to 99.97 per cent of particulates measuring 0. 3 µm. This is particularly beneficial in applications where dry smoke is created, such as when using neat oil metalworking fluids. Designed to meet all European standards and surpassing the Euro F8 and F9 limits, the oil mist filters make use of a pre-filtering system using the principle of wind shear to separate oil, smoke, haze and toxic aerosols, the oil is then separated for recycling. Filter performance is monitored by a pressure gauge and Carbon filtration module (active carbon module available as an option) which can be replaced quickly and easily when required.
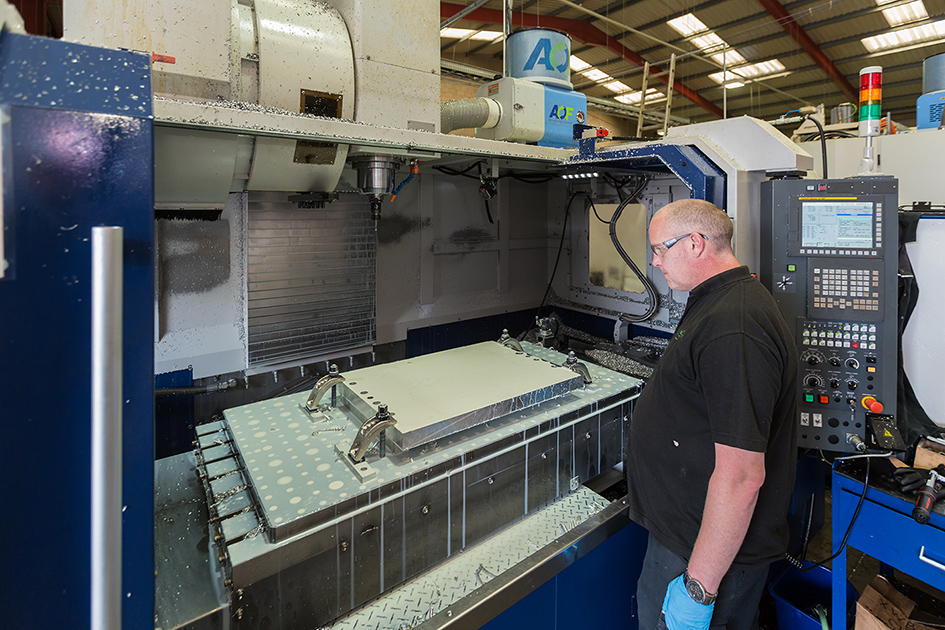
Oil mist filtration system supplied by Matchmaker CNC are improving the environment and productivity at Nasmyth Arden
Machine utilisation is also important to Nasmyth Arden and here it was recognised that expensive machine time, particularly on its five axis machines, was being used simply for roughing operations. Addressing this Alan Lucas turned again to Matchmaker CNC for a solution. “We needed a machine with power and capacity to rough out these billets of material, it needed to be capable and cost-effective and Matchmakers solution of a TongTai TMV1500A vertical machining centre fit the bill. With its 10,000 revs/min, BT40 spindle, and 1525 mm x-axis, we could machine everything we needed to on it, using it for all of our pre-op work prior to transferring it for finishing on the five-axis machines.”
The time savings that Nasmyth Arden is achieving are significant with a typical aluminium chassis taking 23 hours to fully machine on the five-axis machine, this is now broken down to three hours roughing on the TongTai three-axis vertical machining centre, then finish machining taking 13 hours on the five-axis machining centre. A saving of seven hours per component, or roughly a day of production. “The addition of the TongTai TMV1500A has given us a metal removal capability, improved process times across the factory and also increased our overall flexibility as we can manage throughput much better by not tying up the high value five-axis spindles we have.”
In addition to its 10,000 revs/min, 11 kw, spindle (8000 standard) the Tongtai TMV1500A also features rapid traverse of 18 m/min, and feedrates of 10 m/min in all axes, 24 position cam-type toolchanger, and door openings that allow ease of access for craning larger components onto the 1600 mm by 762 mm table. While the benefits of health and safety in regard to oil mist extraction have been recognised for some time, the time savings that Nasmyth Arden are experiencing as a consequence of fitting these units to their high performance machines is also a major consideration in their application, Matchmaker CNC envisages a time when all machines will be fitted with system such as this and, with the technology involved with the Matchmaker system, along with its price/performance ratio the cost of retrofitting is no longer a real barrier to gaining these benefits.