The AMB exhibition this week will see the European debuts of two major new product ranges from Hardinge Inc., both of which feature significant design and manufacturing innovations.
The new developments are the Talent P high performance turning centres and the Bridgeport XT travelling beam five axis and five face vertical machining centres.
Both ranges have been developed by Hardinge using the Global engineering footprint which extends across all continents accessing years of design experience and the manufacturing ability to produce industry leading products.
This philosophy combined with the Six Sigma program within the Hardinge Group ensures the latest complex products are produced to the same high quality across all of its operations, worldwide.
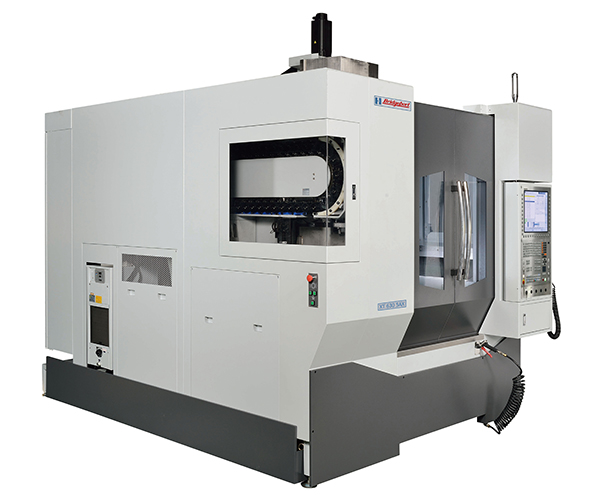
Hardinge XT 630 5AX
The Talent series machines currently offer two structures (for short and standard lengths) built on a robust one-piece cast iron base with heavy duty roller linear guideways and ball screws.
As standard the machines are supplied with ANSI configured Collet Ready spindles available in a choice of 42 or 51mm capacities. There is also a collet ready sub-spindle with a 42mm through hole capacity.
Other standard features of Talent machines include through tool and headwall air/coolant for both main interfaces and a chip conveyor and bar feed interface. The standard controls are Fanuc OiTF and Siemens 828D.
The Bridgeport XT is the first milling product realised through global engineering and fully complies with the latest ISO Standard 16090-Pt.1 with Functional Safety and the design adopts a travelling beam structure resulting in exceptional geometric accuracy. This design incorporates the 3 linear axes with the cutting tool combined with the rotary and tilt axis table supporting the workpiece.
The innovative travelling beam design represents the first of a new generation of 5 axis machining centres from Hardinge. A large capacity Ø630mm trunnion table with capacity of 350 kg, coupled with 900mm swing diameter extends the range of Bridgeport 5 axis solutions. The design and use of twin drive tilt axis maximises the drive stiffness and resulting in high precision.
Thermal distortion effects are minimised by chilled spindles, cooling of ball nuts and end bearings in all linear axis optimising machining accuracy. Heidenhain TNC640FS and Siemens 840Dsl SI controls with 19” operator screens providing highly optimised 5 axis motion, and for 5 face operation both Heidenhain TNC620 and Siemens 828D are incorporated.
On the new introductions, John McTernan, Managing Director, European Sales & Marketing for Hardinge Inc. comments; “These are genuinely ground breaking machines which exemplify our commitment to producing the highest quality machines for worldwide markets which are in the tradition of Hardinge and Bridgeport.
“Hardinge has assembled a global design team based in the USA, the UK and Taiwan and the team has addressed many fundamental aspects of design criteria to create these new machine ranges. The result will be families of machines making use of the economies of scale by standardising elements of the construction to create highly competent performance alongside competitive pricing.”