LMS Precision Engineering has trusted its tooling supplier for over 35 years. With a relationship that dates back more than three decades, many manufacturers would ask ‘why?’ The simple answer lies in the fact that Midlands-based LMS works with Guhring UK, one the world’s leading manufacturers of cutting tools with UK manufacturing facilities and expert engineers on hand to deliver optimal machining solutions, whatever the challenge.
Scott Street, a partner at Droitwich-based LMS Precision Engineering says: “We are a family-run business that has been operating for over 40 years. Our main sectors of interest are aerospace and general subcontract machining. We have always had a great relationship with Guhring.”
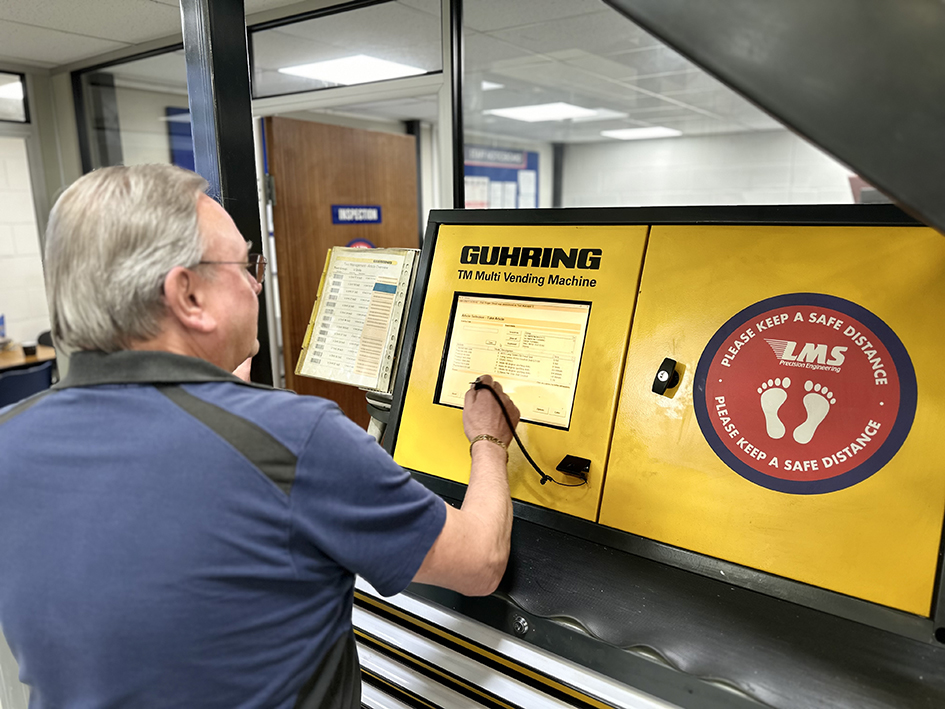
The Guhring Tool Vending Solution at LMS
Discussing the relationship, Chris Bush from Guhring says: “LMS and Guhring have been working together for over 35 years now. LMS use the whole spectrum of our cutting tools, whether that’s milling cutters, drills, taps or thread mills. In fact, everything through to the Tool Management vending machine. LMS were one of the first customers to see the advantages of a tool management vending machine. Allowing them to put their resources in providing components rather than manually ordering tools, looking for tools and managing tool stocks. The TM machine automated all this and much more. The relationship has evolved so much over the years. In that period, cutting tool technology has changed and evolved hugely, as has the LMS business, the technology it invests in and the size of the company. The customer base at LMS has evolved as well, and they are machining a lot of different materials, so down the 35-year relationship – it has been exponential growth and change on both sides. However one thing remains, and that is the strength of our partnership.”
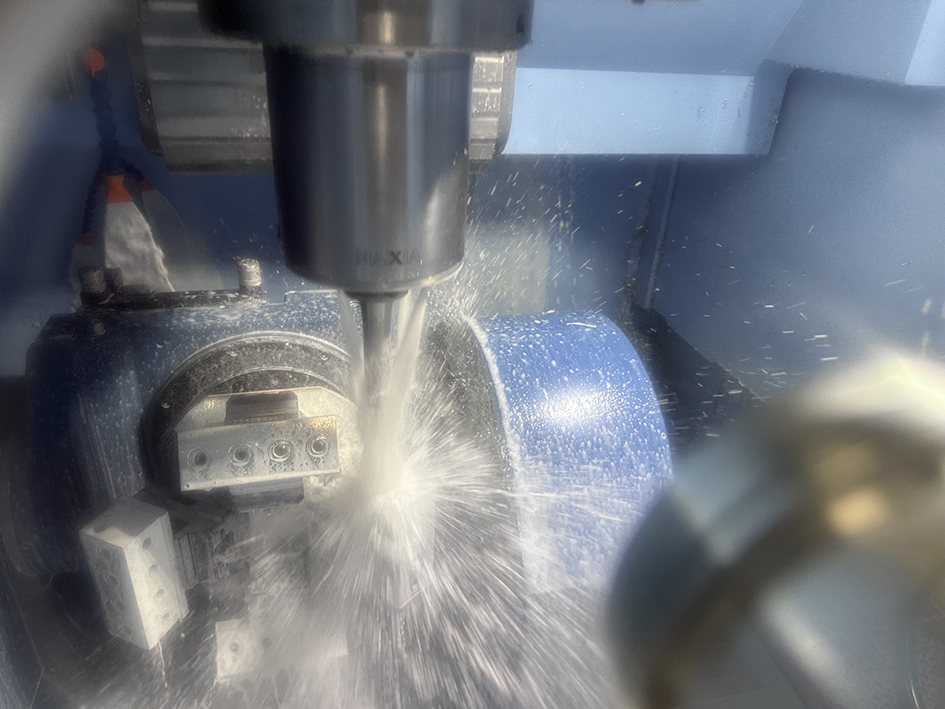
Guhring tools in action at LMS
The Guhring Tool Management vending solutions can be built to a customer’s requirements and are available in open drawer type for maximum versatility or 100% secure single tool dispensing. The system will control and monitor tool consumption and spending with reporting for complete visibility. The main benefits of the Guhring Tool Management vending solutions include 24/7 controlled tool availability and prevention of production stoppages due to tool availability. It will also eliminate loss and theft, create employee awareness of tooling costs and the system can communicate with customer IT systems.
Recalling specific product lines that have supported LMS Precision, Scott continues: “We had a lot of joy with the Guhring VA Series drill and now there is the new InoxPro drill as well, so this is bringing us even greater runtimes than ever before. We use Guhring on everything, from end mills such as the high-speed rippers, the through coolant drills, high-speed steel drills, stub drills – absolutely everything.”
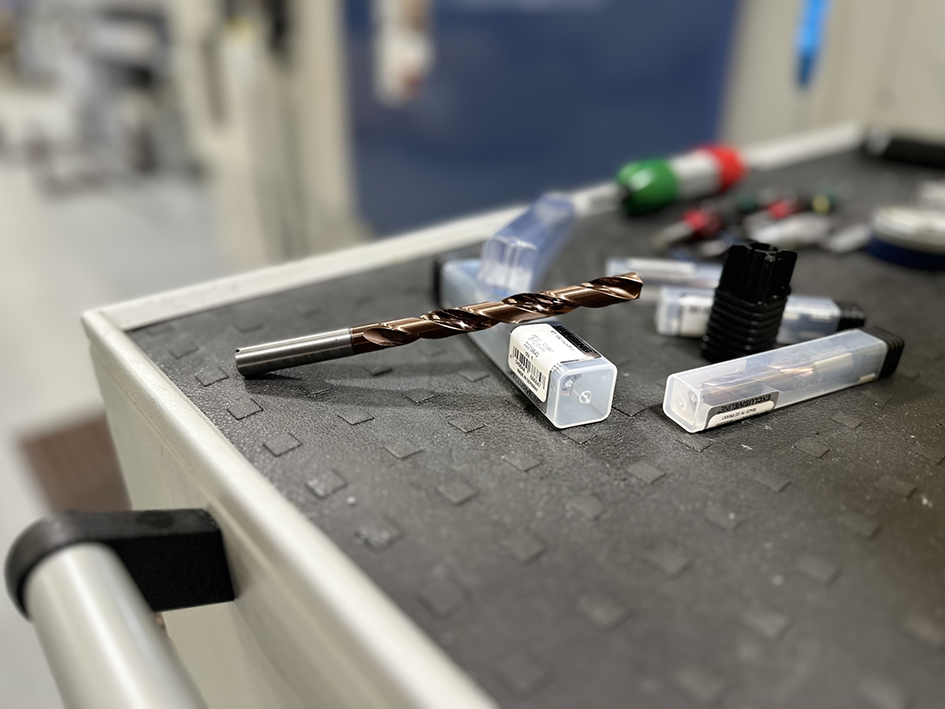
The Guhring drills are making significant improvements at LMS
Adding to this, Guhring’s Chris Bush says: “LMS use a complete range of our tools and they machine so many different types of material, they have to have material specific cutters as well as general-purpose cutters. They use the whole spectrum of our tooling range. With the range of stainless steel that LMS machines have; the new InoxPro is perfect for them. The Inox Pro introduces a new grade of carbide, so it is a much tougher carbide with a new geometry that is specifically for titanium and stainless steel. We also have the new Perrox coating on there as well. This is a much tougher wearing coating that is a lot smoother and this delivers optimum swarf evacuation.”
“The benefit of using Guhring as a supplier is that we manufacture our carbide. We can make our own grades for specific applications, so we have made tougher grades of carbide that are not as brittle as carbides from other manufacturers. This makes it perfect for challenging applications in titanium and stainless steel.”
Alluding to the application of the latest generation of tools, Scott comments: “The latest tools have given us the confidence to run lights-out, reducing the number of tools we need to stock and giving us full visibility of all tool usage and tool performance. This is especially the case with the VA Series drill. With that drill, we can now run over 1200 parts over a period of 15 hours on 316 stainless, drilling a 10mm diameter hole at 17.65mm deep with no problems at all. It’s absolutely great. The confidence it has given us is incredible. We have worked with Guhring for 35 years, and the products and support are great. The relationship we have and the products are brilliant.”
Concluding on the partnership, Chris Bush continues: “We have built a brilliant relationship and we are looking forward to the next 35 years. LMS have got exciting new projects coming through and new machines that they are investing in. Combining their technology and the advancement of materials, there will be plenty of exciting new challenges ahead and we relish the opportunity to deliver results long into the future.”
Leave a Reply