Founded in 1984 and having moved repeatedly to larger premises to cope with almost continuous growth in turnover, subcontractor Norjon Precision Engineering expanded yet again at the end of 2018 with the acquisition of an adjacent unit on the Quay West Business Centre in Gosport, which enlarged the factory to 17,500 sq ft. Alongside this increase in shop floor space, the firm has invested substantial sums year on year, with £2 million spent during 2018 and 2019 and £1.2 million of capital plant on order for delivery during the first quarter of 2020.
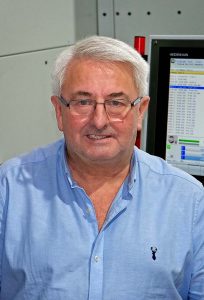
Kevin Fox, owner and managing director of Norjon Precision Engineering.
A pivotal moment in the accelerating rate of Norjon’s development was the decision in 2016 by owner and managing director Kevin Fox to automate a large proportion of production. The latest machine acquisition was a Hermle C 400 5-axis milling centre fitted with the manufacturer’s HS Flex automated storage and retrieval system for eight 500 x 400 mm pallets. The turnkey cell, with touch-screen control for smart order management and connectivity for remote monitoring, was supplied in October 2019 by UK, Ireland and Middle East agent Kingsbury.
It joined two automated Hermle 5-axis cells delivered in 2018, a C 22 U and a C 12 U, both equipped with Erowa storage systems for exchanging smaller pallets. A further Hermle C 12 U is to be delivered in February 2020 equipped with a Dutch-made Halter robotic system for automated component loading and unloading around the clock, initially of vehicle engine parts. In total, taking into account three Hermles bought in 2017 and 2018 and legacy models from 2007 and 2012, plus a mill-turn C 42 U previously used by the AMRC and a larger C 52 MT mill-turn with a one-metre table due to arrive in March 2020, Norjon operates nine of these German-built 5-axis machines with a further two on their way from Kingsbury.
Mr Fox commented, “In 2016 we often made batches of six-off prismatic parts of fairly high complexity. Even though we are a long-time user of 5-axis equipment, which helps to make components in one hit and mitigate some of the time and cost of manufacture, it was easy to lose money on those jobs with all the programming and setting that was needed.
“So we took the decision three years ago to go after contracts for much larger batches of components, more like 50- or 60-off, but still complex in nature requiring substantial machining time.
“Then one of our established customers in the medical industry ordered larger volumes of parts that we were already making. It was the trigger for us to move towards automation with the purchase of the first Hermle 5-axis cell.”
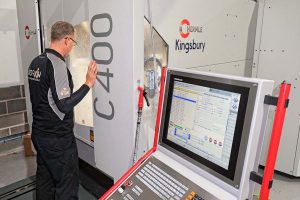
Another view of the Hermle C 400.
He advised that Norjon now operates four automated prismatic machining centres, including one from another supplier, and will soon have a fifth with the arrival of the Hermle / Halter cell. They allow virtually continuous production with minimal operator supervision throughout the night and at weekends as well as during the day. He said the factory really sings now when he goes onto the shop floor, whereas before some machines might not be running as they would be waiting for fixtures or programs. He describes the difference as amazing.
The latest automated cell comprising the C 400 and HS Flex has been installed in the factory extension together with the existing C 20 and a spark eroder. With storage for eight pallets on four levels and extended tool capacity totalling 81 positions, the Hermle was purchased to fulfil a contract requiring the delivery of 10 assemblies per week for a customer in the automotive industry. The two parts, towards the larger end of components produced, require 10 hours’ and 5 hours’ machining respectively from solid aluminium and were initially milled and drilled on an unautomated C 400. Considerable extra capacity has been gained due to the HS Flex running unattended for long periods.
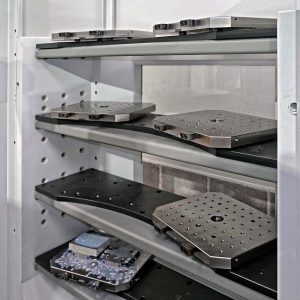
The eight storage positions on four levels in the HS Flex for 500 x 400 mm pallets.
Norjon now concentrates on working for four large corporations in the medical, food, automotive and marine propulsion industries. In the case of the latter sector, it has recently become a preferred supplier to BAe Systems Maritime, which was the reason for installing the first Hermle mill-turn centre, as it allows turning of parts up to 800 mm in diameter and prismatic machining within an 800 x 800 x 550 mm working envelope. The new C 52 MT will extend mill-turn capacity to nominally one metre cube.
Mr Fox concluded, “We started buying 5-axis Hermles back in 2007, as we could achieve an almost polished finish when machining aluminium and brass thermoforming moulds for the production of plastic food packaging.

A view of the robotic transfer arm that moves pallets automatically between the workpiece load / unload station in the background, their storage positions and the Hermle C 400’s working area.
“For our latest round of investment, we have returned to the same manufacturer due to our good experience with their machines over the years, its strong offering in automation involving its own and third-party solutions, and the excellent back-up provided by the sales agent Kingsbury.”