A new, twin-spindle, 10-axis CNC turn-mill centre, the Miyano BNA-42GTY LFV, has been introduced by Citizen for manufacturing complex components in one hit from bar stock up to 42 mm diameter. The hybrid machine is of fixed-headstock design, but the head is also able to move in and out of the working area for extra versatility, similar to that offered by a sliding-head machine operated in non-guide bush mode.
The 8-station, 3-axis turret including Y-axis movement has a half-indexing mechanism that allows tools to be mounted at up to 16 positions, while multiple toolholders can further expand the number of cutters deployed. There is also Y-axis travel on a gang toolpost, giving extra flexibility when machining at either spindle, especially as the counter spindle moves in the X-axis as well as the Z-axis.
In total, up to 45 tools can be resident in the working area. A superimposition function within the Mitsubishi M730VS control provides the possibility for shortening cycle times even more by enabling up to three tools to be in cut simultaneously at both spindles.
The 3.74-tonne BNA-42GTY enjoys the same rigid, high precision build and thermo-symmetrical design as other lathes in the Miyano range, leading to high accuracy machining. Slideways are hand scraped in all axes and have exceptional damping characteristics, enabling heavy metal removal and helping to prolong tool life. Machine specification includes a 6000 rpm / 11 kW main spindle with 0.001° C-axis, a 5000 rpm / 5.5 kW C-axis counter spindle and feed rates up to 30 m/min.
Numerous options are available to add to the flexibility of the turning centre, including high-pressure coolant, spindle air blow, chip conveyor, parts catcher, parts conveyor and drill breakage detection. Likewise, the capable control can be augmented with the addition of helical interpolation, corner radiusing, synchronous tapping and multiple canned cycles.
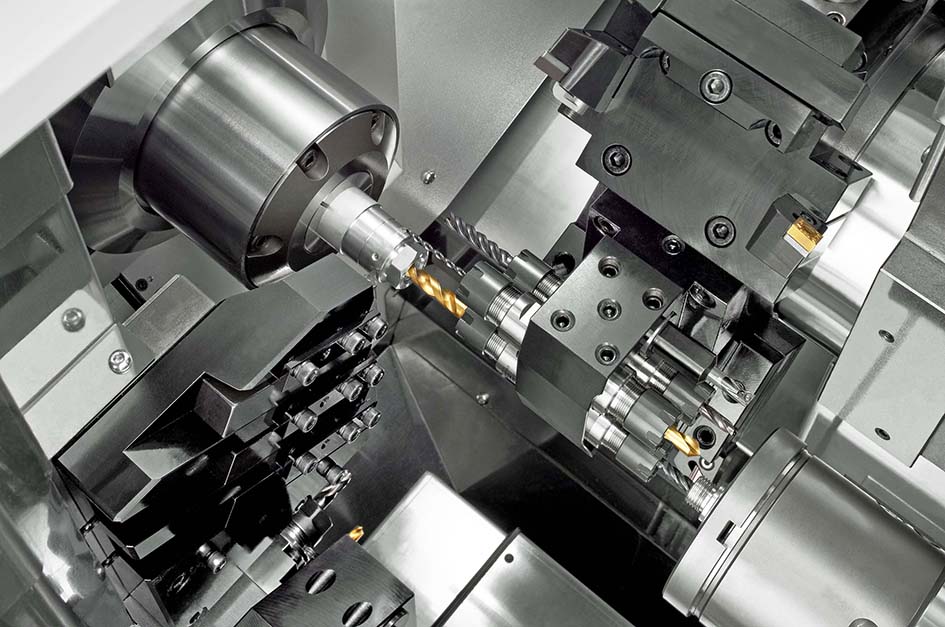
Working area of the Miyano BNA-42GTY LFV.
The BNA-42GTY is the first Miyano machine to gain the benefit of Citizen’s LFV chipbreaking software, until now exclusively provided on the manufacturer’s Cincom Swiss-type lathes. The patented, two-axis chipbreaking functionality is part of the control’s operating system and involves the axis servo drives and spindle drives.
The position of the tool tip is oscillated by 20 microns, just sufficient to break the swarf. The number of oscillations per revolution (mode 1) or the number of revolutions per oscillation (mode 2) determines the length of the swarf removed from any type of material. The user can define the exact chip length in the program, giving the ability to choose the optimum size for the swarf conveyor to handle efficiently.
The more exotic and difficult to chip the material, the more effective LFV is. It means that high pressure coolant is not needed to assist in breaking long stringy swarf, such as that generated when machining such materials as stainless steel, copper and plastic. So it is no longer necessary to stop the cycle to remove accumulated swarf that is hampering the machining process. Shorter chips also take up less room in the swarf bin, so it needs emptying less frequently.
In some applications, particularly when processing exotic materials, productivity can be increased fivefold due to not having to stop the machine repeatedly to clear swarf that has entangled itself around the tool or workpiece, or both.
With LFV there is an element of air cutting, which allows more coolant to access the point of contact between the tool and the material. Enhanced coolant penetration lowers the operating temperature of the tip, so it can last five or even 10 times longer. This is especially the case if, as frequently occurs on other makes of CNC lathe, a chipbreaking macro has been written into the program. These are notorious for causing rubbing of the tool, built-up edge, machining inaccuracy and premature failure of the tip.
An LFV oscillation results in a turned face that is no longer flat by an amount measured in microns. The machine control knows where the oscillation took place and on the second revolution the high spot on the face is turned away. If required, on the third revolution the tool will finish that process to eliminate the waviness completely at that location.
As an element of air cutting – albeit miniscule – is introduced by LFV, productivity can be slightly reduced when the function is switched on. However, it can be turned off at the control, allowing the possibility of maximum output during attended day shifts when an operator is present to clear swarf. It may be, however, that these machine stoppages lower production output by more than LFV.
Switching the function on at night allows a ghost shift to be instigated without fear of swarf build-up automatically halting production during unattended running. So a manufacturer is virtually guaranteed a full shift’s worth of good components on arrival the next morning.