Automotive supplier transports 1200 ° C hot steel blanks with scale formation on toothed chains.
Boiling heat, scaling and fouling characterize the forming process of steel.
This is also the case in the Hirschvogel Eisennach GmbH factory for the massive forming of steel from blanks. The automotive supplier needs a long-lasting and safe solution for the transport of hot steel blanks and therefore relies on Renold tooth chains
Challenge chaining
Hirschvogel Eisenach works independently, plans new plants, parts and tools himself, has its own department for toolmaking in-house and around 40 employees in maintenance alone. While large machines such as die forging and presses are designed for harsh operation and work smoothly, the concatenation of a new system has created massive problems. “By the year 2004, we had slab tapes in operation, which worked well in the first small-scale production, but in the hard multi-shift operation soon caused disturbances by deformations, leadership problems and terminals,” explains Dennis Reinhardt. “Then we looked for an alternative means of transport and came to Renold’s tooth chains”
In Marksuhl, south of Eisenach, raw materials with a diameter of 20 to 40 mm and a length of up to 400 mm are processed in the steel area with numerous variants of the finished products. After the blanks have been aligned in the bunker and transported to the annealing furnace, the first transport chain is used: heated to 1,200 ° C, the workpieces are removed from the spool, the temperature is sensory-measured and the “well-tempered” parts are glistening red on the Renold transport chain , which conveys it further for forming in the round jaw roller. The rolling process is followed by the next Renold tooth chain, from which the parts are transferred to the forge by means of a parallel transfer. Finally, the rolled, forged workpieces are deburred.
Heat, scale and release agent
“The interlinking of steelworking machines is a huge challenge,” affirms Dennis Reinhardt. The reasons for this vary: first, the 1,200 ° C hot parts are directly on the transport chain, so that it must be absolutely heat-resistant. The Renold transport chain solves this problem by their involute teeth, so that the chain does not expand despite the heat.
Furthermore, aggravating added that form on the surfaces of the steel parts by heating oxide layers and this scale then peels off. The tinder is hard and crumbles and settles like salt in the joints. Therefore, additional cleaning discs are used, with which the chain is cleaned with each deflection over the gear, so that the scale falls out and cannot stick to the chain. Dennis Reinhardt comments on these conditions: “That’s what a chain has to endure. Here, the statement of functional reliability and long service life due to low wear reaches a completely new dimension. We can only confirm both here. ”
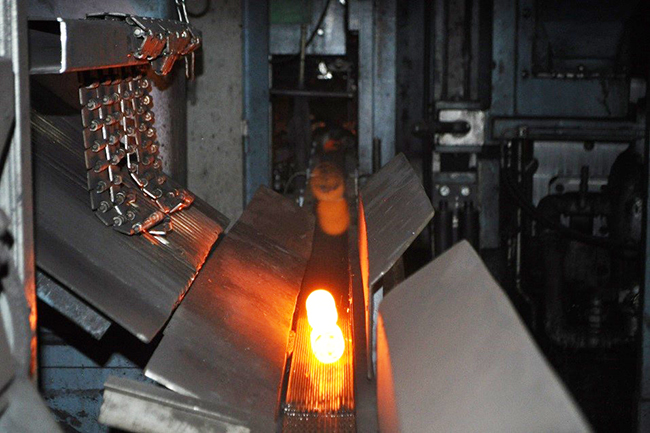
Tooth chain transporting the 1200 ° C blanks
Delivering quality products on time and reliably is a top priority for automotive suppliers. For this reason, the cost-optimized production of massively deformed components often requires special arrangements.
“In doing so, we always have to look at the entire value added chain from the blank to the finish,” emphasizes Dennis Reinhardt, responsible for maintenance at Hirschvogel Eisenach GmbH in Marksuhl. “We work partly in 4-shift operation. The high speed of work and the difficult conditions of use must, of course, withstand all machinery and equipment. “
As a member of the Hirschvogel Automotive Group, Hirschvogel Eisenach GmbH concentrates in its production on the massive forming of steel from round material as well as aluminum from extruded profiles. The company mainly produces vehicle parts such as wheel carriers, control arms or pump housings for well-known automobile manufacturers.
High-alloyed, stable and fast
The Renold tooth chain for high-temperature applications consists of a high-quality tempered steel. The sprockets are made of high-alloyed tool steel with natural core strength, which is additionally vacuum-hardened. Hirschvogel Eisenach uses the transport chains in the standard widths of 85 and 100 mm, of which the longest chain measures 10 m with a center distance of 5 m. The chains run here without lubrication, as a lubricant in the hot environment char and thus could cause even more pollution or wear. Due to the high production rate of 15 seconds, the chains move despite the sliding friction on the sliding bed at 1m / sec at high speed. “That’s why they have to run at such a high speed because the heated parts would otherwise cool down on the approximately 5 m long path between the annealing furnace and the press and would then be unworkable,” Reinhardt adds.
Dipl.-Ing. Werner Weber, owner of the engineering office Weber in Heilbad-Heiligenstadt, put out the transport chains for the Marksuhl plant. “To be on the safe side, we duplicated the middle guide of the transport chain so that each chain link now has a guide that engages in the groove of the sprocket,” he explains. There were good reasons for the continuity: both the long wheelbase and the workpieces slid across the conveyor belt, which could push the chain to the side, were the decisive criteria. At the same time, this extension causes the wear of the guide plates is reduced and their life is increased.
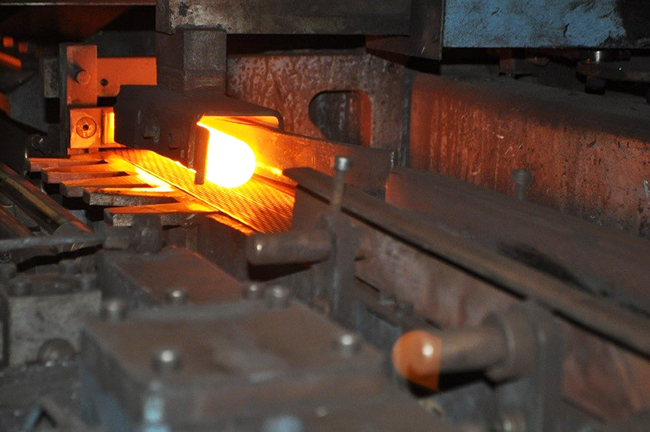
The toothed chain moves at a high speed of 1 m / s. The parts should not cool down on the way to the pressing machine
The Hirschvogel components are often key components for transmitting forces and moments or for certain functions in the target system, such as antifriction bearings for friction minimization in the engine. The requirements regarding product quality, safety and delivery times are correspondingly high, so that Hirschvogel places equally high demands in the selection of the systems.
7 maintenance shutdowns saved
As an automotive supplier, Hirschvogel has to continuously produce Eisenach, prevent unplanned plant shutdowns and ensure reliable means of production. Therefore, the tinder accumulation and the forging necessary, hardening release agent particularly stressed chain was divided. The part leading directly to the machine can now be simply pulled out on a stand and cleaned every week.
Dennis Reinhardt sums up the positive changes that have occurred in terms of maintenance through the use of Renold transport chains: “Previously, we had to replace the conveyor belt every three months because the teeth were rubbing off on the pinions. Each time nearly six hours of production time have been lost through removal, cleaning and assembly. In contrast, we now plan the chain change in the context of the scheduled annual maintenance of the system, keep the required 7 maintenance shutdowns saved material and thus save seven maintenance downtime only in terms of the means of transport. ”
In addition to the transport chains for the glowing hot workpieces, Hirschvogel Eisenach also uses another Renold toothed chain with a width of 270 mm for transporting pallets. Due to their high shear and flexural strength, the chain can easily withstand the heavy pressure of the heavyweight goods.
Renold Chain European Sales, Trident 2, Trident Business Park, Styal Road, Wythenshawe, Manchester M22 5XB, Tel: +44 (0)161 498 4600 www.renold.com