Walter Ewag UK, a member of the United Grinding Group, reports that a number of machines from the Walter Helitronic tool grinding/erosion and Walter Helicheck tool measurement machine range, as well as Ewag’s Laser Line Precision insert production machine, will be on view at AMB, Stuttgart.
Visitors to AMB will, therefore, have the ideal opportunity to see for themselves the build quality of these machines and, of course, also be able to investigate the numerous technology features available to help improve productivity and quality levels in terms of both tool and manufacturing and regrinding, as well as tool inspection and insert production using a laser.
From the Walter Helitronic range of multi-axis tool grinding/erosion and regrinders, on show will be the two-in-one Power Diamond 400 grinding/erosion machine with robot loader – for the production of PCD as well as carbide tooling – and the Power 400 tool grinder/regrinderwith robot loader.
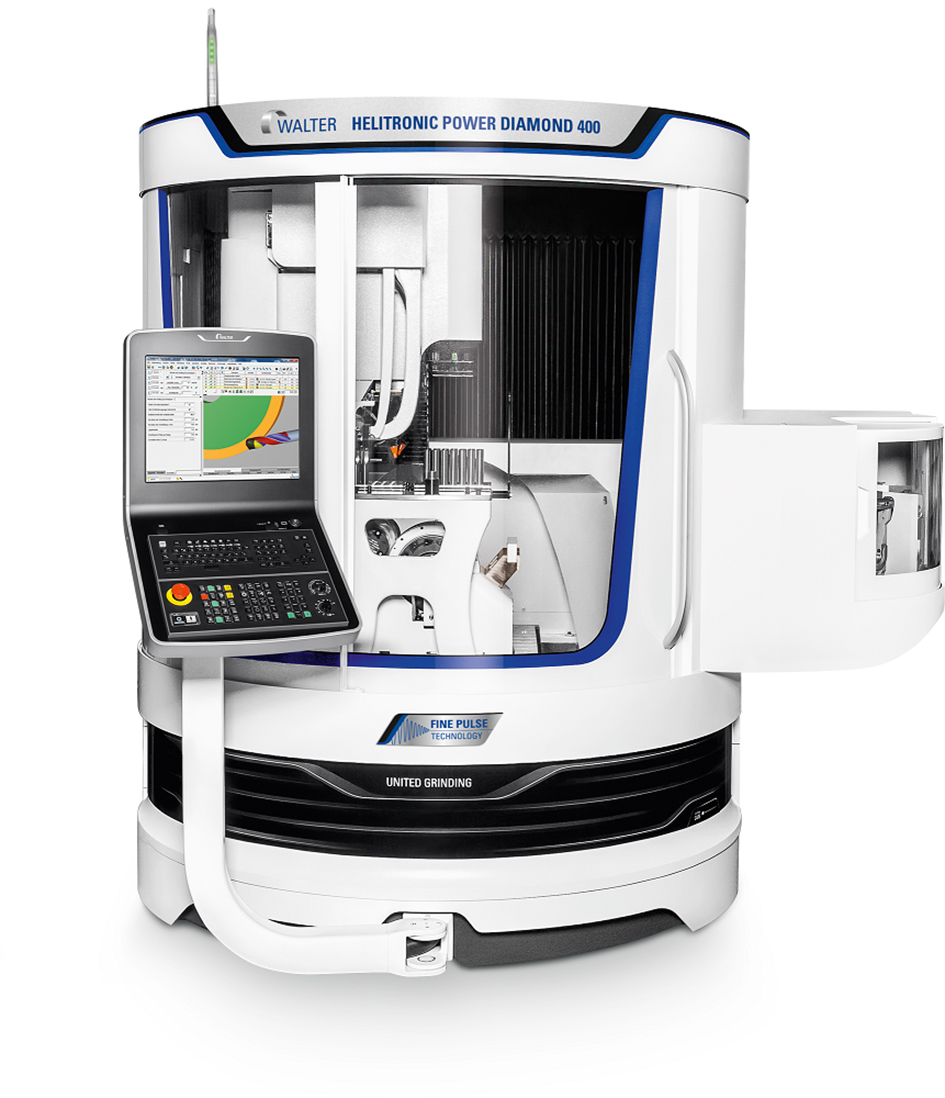
The Walter Helitronic Power Diamond 400 will be shown with a Robot Loader
Both machines can accommodate tools of 3 mm to 315 mm diameter and up to 380 mm long, and in addition to having a grinding wheel/electrode changer (four-station as standard; eight-station optional) for increased automation and unmanned operation, both can utilise a range of robot loading solutions – the Top Loader for up to 500 tools, a Robot Loader for up to 7,500 tools or a Robot Loader 25 which has a capacity for tools weighing 25 kg including grippers.
Walter’s renowned Tool Studio 3 software will also be available, and this has integrated wizard technology for fast tool production simulation, parameter changes and machine operation – including an erosion function option for the fast and easy programming of ‘what you see you can grind and erode’.
Complementing these will be the Walter Helicheck Plus tool measurement machine with robot loader and the Helicheck 3D.
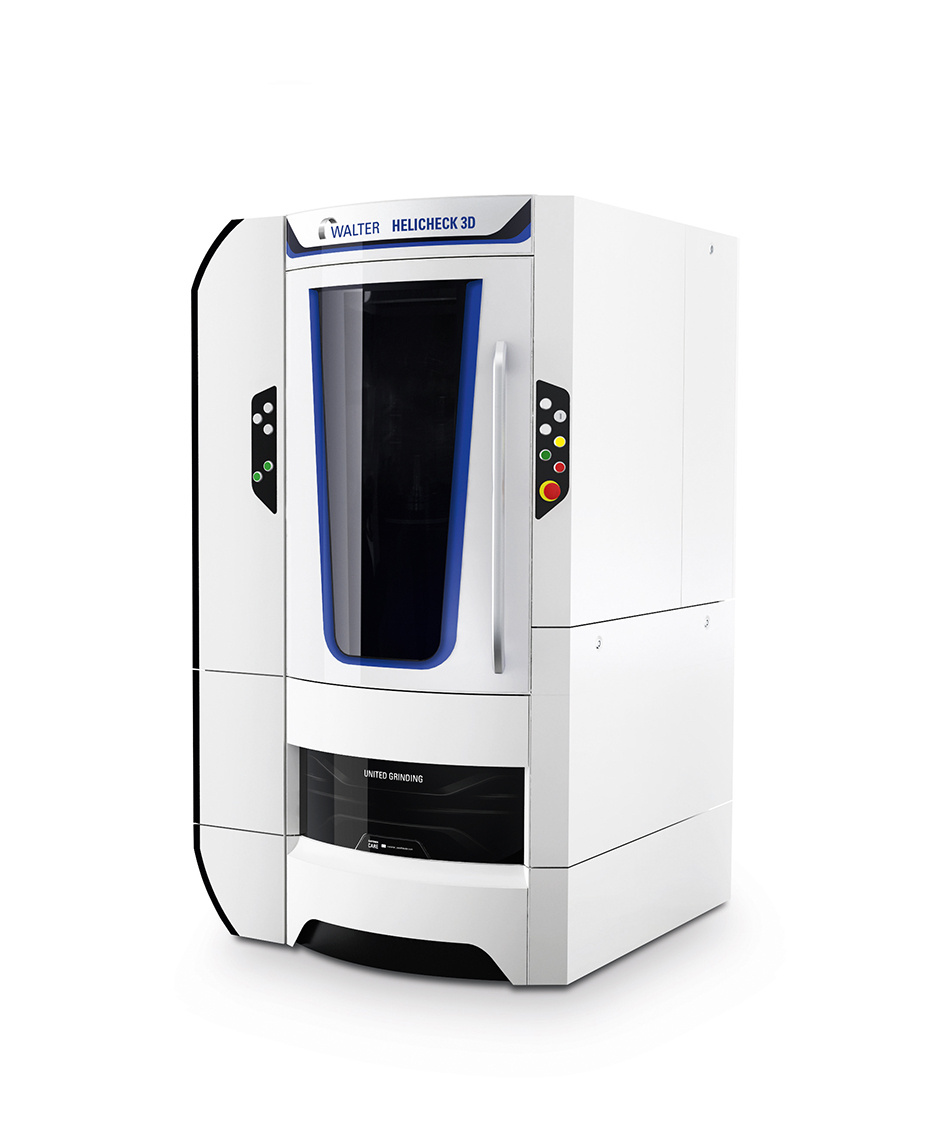
Walter Helicheck 3D
The Helicheck 3D digitises tools and production parts to create three-dimensional model data that can be saved, processed, analysed and measured. The machine utilises a revolutionary new method of digitising to enable items to be scanned and digitised quickly and easily.
Its 3D Tool Analyser software – specifically developed for the application – can lay horizontal, vertical and freely selectable cutting planes at any position on the 3D model. These are automatically analysed and the resulting parameters made available for use.
The capability to measure all important tool features has never been quicker or simpler than with Helicheck 3D and since measurements are carried out on virtual models, the process can be performed offline.
Complementing the machine is a software 3D ‘matcher’ to enable users to create a colour-coded comparison of two 3D models within the machine’s graphical user interface. After the ‘match’ of both models, the operator instantly receives an evaluation of the quality of the products and any deviations from desired values.
The five-axis Laser Line Precision will be representing Ewag’s wide range. This is a cost-effective and highly accurate entry-level machine for processing all commercially available diamond cutting materials including CBN, PKD and CVC-D. The machine can accommodate rotationally symmetrical tools of up to 200 mm diameter and up to 250 mm long, as well as indexable inserts with inscribed diameters from 3 mm and circumscribed diameters up to 50 mm.
Laser Line Precision utilises modern short-pulse fibre-laser technology in the green wavelength range (532 nm) for highly efficient and effective machining, with the resulting flue gas and vapourised material being suctioned away to a suction/filter system.
Incorporating the innovative and patented Laser Touch Machining process, the result is excellent surface quality, even on tools with complex or delicate geometries. Indeed, any type of cutting contour, clearance and three-dimensional chipbreaker geometry can be produced in a single clamping operation.
With a footprint of only 5 m2, Laser Line Precision is the most compact and cost-efficient laser production centre available for super hard tools. An optional six-axis robot offers the highest levels of flexibility during minimally manned, multi-shift operation.