Having started like many with an idea and a garage to work out of, Ian Bamford and his wife Nicky created their business Tuskguard, to design, manufacture and install, physical security products and access control systems, winning a DTI Design against Crime award in 1989. As the business developed, Tuskguard won a prestigious five-year contract at the Houses of Parliament which was using a unique Key based electronic access control system, integrated with bespoke locks designed by Tuskguard that satisfied English Heritage’s requirements for the site. This led directly to the purchase of their first XYZ machine tool, a DPM bed mill with ProtoTRAK control, the efficiency of that machine meant that it was paid for within the first part of the contract, the DPM remains an important and active part of Tuskguard’s capability to this day.
Upon completion of his apprenticeship at the Atomic Weapons Establishment, Ali Bamford, Ian’s son, joined the business and put to use his design background. The result was the creation of a hi-tech pan and tilt surveillance camera, used for asset protection in remote locations. This camera, capable of reading car number plates at between 2 and 3 miles distance and distinguishing people at up to 30 miles away was made up of 1000 components, so additional machining capacity was called for. At the time, XYZ Machine Tools had just launched its innovative LPM machining centre fitted with the Jergens Ball Lock fixture location system. “We had suffered with issues relating to subcontracting work and we wanted to be able to manage all of our machining in-house and control our production schedule,” says Ali Bamford, Tuskguard’s Design and Production Manager. “The ability to quickly change pallets on the LPM and be setting one job while the previous one was in the machine was a major advantage. We were able to manufacture fixtures that could hold multiple parts and run for 18 hours unattended, producing hundreds of parts in one set-up.”
At the same time as the XYZ LPM was delivered, Tuskguard also took delivery of an XYZ SLX 355 ProTURN lathe, which combines the ability to operate manually, but with the knowledge that the ProtoTRAK control can be used for more complex one-offs and small batch runs. “The combination of the LPM and SLX were perfect for our business model, which we see as a one-stop-shop for customers who either have finished products they want machining in volume or a design project where prototyping is required; which we can then take through pre-production, to the finished item” With a slowdown in demand for the camera system the search was on for alternative products to manufacture and with Ali shooting for a hobby, the decision was taken to create a sister company, Calibre Innovations, with the initial aim of developing and manufacturing a range of suppressors/moderators, commonly referred to by Hollywood as silencers.
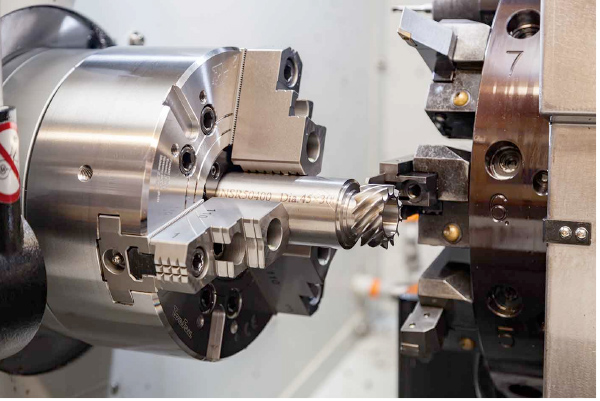
The XYZ CT52 LTY is allowing more complex designs to be manufactured more efficiently by Calibre Innovations
The initial concept was brought to reality by creating the components in plastic using a 3D printer that the company has. While this worked and was successful, the long-term development meant that manufacturing out of more robust material that could withstand the gas pressures when the gun is fired, was required. The principal behind a suppressor is to disrupt the gas flow and slow it down, thereby reducing the noise. Initially the design was for small calibre .22 weapons and then Ali developed a model for centre fire (larger calibres) weapons. This involved a more complex baffle inside the suppressor that would require y-axis turning capability. With three XYZ machines already in place the choice was to go for an XYZ CT52 LTY turning centre. While this was a move away from the familiar ProtoTRAK control fitted to the DPM, SLX and LPM machines, the ease of use of the Siemens control made it a straightforward move. The 52 mm bar capacity was perfect for the titanium bar that was to be machined and the +/- 35 mm y-axis travel allowed the complex turbine form on the baffle, designed to make the gas work and travel further within the suppressor, to be machined.
“The arrival of the CT52 LTY allowed the design of the current Ducis suppressor, which is made up of four interchangeable baffles, with varying thread sizes to allow modular fitment to different guns and for different applications. We couldn’t manufacture this efficiently without the Y-axis. The alternative would have been two operations on the SLX then transfer it to the DPM mill and use a manual dividing head to produce a much simpler form. Now it is one operation on the CT52 LTY with a small second operation to drill location holes on the LPM,” says Ali Bamford.
With the arrival of the CT52 LTY, Calibre Innovations was also able to expand its services relating to the manufacture of custom/bespoke rifles, based around the Armalite AR 10 and AR15 platforms. With the capability and versatility provided by the XYZ CT 52 LTY and LPM machining centre it is a quick and easy process to develop custom parts. The success of the suppressors and other work undertaken by Calibre innovations has seen it overtake its originator, Tuskguard, in terms of turnover accounting for around 80 per cent of total sales of the two businesses.