The highly specialised grinding section within the Bodmin, Cornwall moulds and tooling manufacturing operations of West Pharmaceutical Services Cornwall Limited has maintained its loyalty to Jones & Shipman grinding machines following an investment and upgrade programme.
Recently installed are a Jones & Shipman Ultramat 650 EASY cylindrical grinder, two J&S 524 EASY surface grinders, and a Hauser H35 jig grinder–also supplied through Jones & Shipman.
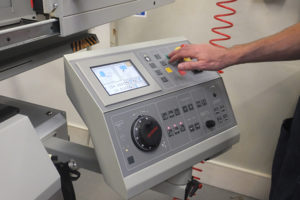
The J&S touch screen control with EASY software.
West is a market leader in the development of pharmaceutical packaging components and delivery systems for injectable drugs. It prides itself in being at the forefront of pharmaceutical and biotech innovation, developing new therapies that will become tomorrow’s healthcare solutions.
In Bodmin, the extensive toolroom operation reflects the standards of the pharmaceutical industry – the machine tools and environment are spotless – and as John Chaffe, Manufacturing Manager at the plant explains, there is a culture of not just cleanliness but absolute precision.
“Consistency, accuracy and surface finish are the mantras across everything we manufacture, says Mr. Chaffe. “Mostly we work in stainless steel with rubber mould manufacture predominating and these are bespoke to the many moulding machines in operation in West’s worldwide operations.”
“Primarily the mould consists of two matching plates containing inserts which create the seals or stopper vials. Plates can accommodate anything from a few hundred inserts to the very largest we manufacture which contains 11,000,” he explains.
“There is no compromise on precision or quality and component repeatability is a major factor which frequently necessitates complex ground surfaces to low micron finishes. We always flood the component and work table in coolant,” he adds, “a time proven way of negating thermal expansion.”
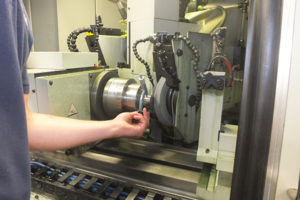
The Ultramat 650 EASY is fitted with a B axis.
As well as rubber moulds in many formats, the Bodmin operation also manufactures plastic moulds for products such as tamper-proof tips; very fine ground cones for producing needle shields and trim dies used for precision cutting the finished seals after moulding.
High grade stainless steel is the first choice work piece material for both the surface finishes achievable, and also because of the arduous sterilizing regime that involves submersing the moulds in 400ºC saline solution.
And, as John Chaffe explains, Jones & Shipman has long been the preferred grinding machine supplier to West in Bodmin. “We have operated two older 1300’s for some years, but when it came time to upgrade, we were impressed with the EASY software J&S has developed for programming and operating its latest generation machines. We first invested in a 524 surface grinder with the touch screen and EASY software, and when we added another 524 along with an Ultramat EASY 650 cylindrical machine, they readily integrated with our manufacturing processes.”
Operator acceptance of the EASY software has been excellent, and while the many different programmes are accessed from a network, skilled and semi-skilled operators alike find the software used at the machine “easy” as its name suggests.
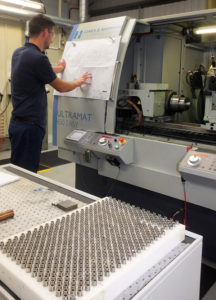
Repeatability for inserts manufactured in batches is all important.
The latest generation Ultramat 650 specified by West, features the optional B axis with its wheelhead swivel for grinding negative tapers. The B axis provides the ability to not only grind multiple diameters but to angle features on components in one process and to automatically external and internally grind in one set up. This not only improves the cycle time but also the important repeatability and concentricity of parts as the component does not have to be remounted when undertaking batch work.
Another specified option is an ACL (acoustic listening device) which allows very precise pick up by the operator when the wheel touches on the part. It is very accurate and allows the operator to run the machines to micron accuracies. There is also a special adaptor to accommodate occasional polar grinding.
The Ultramat 650 design features a one piece “Tee Bed” design with a fully supported table combined with technical innovation and the ability to offer high geometric accuracy.
The control panels have membrane-type touch keys and electronic handwheels, while the machine also has automatic dressing and grinding cycles which means it can be quickly set, then left unmanned.
As standard, it is equipped with Heidenhain® “Absolute” Nano linear scales and Fanuc® Digital AC servo motors and control.
Jones & Shipman Hardinge is a Hardinge Grinding Group company.
For UK enquiries please contact Jones & Shipman Hardinge on +44 (0) 116 201 3000 or e-mail sales@jonesshipman.com